Hi everyone!
In advance, I want to say sorry for my English, especially for the technical expressions, they can be inaccurate sometimes.
Would you consider Bearing Resistance of the plate in a connection like the one below when we design the connection for axial load in the stud(Stud and Track of a light gauge steel residential structure) or we consider that the web of the stud and the track are connecting, and the axial load is transferred at the whole surface, not only at the fasteners? If I consider that the whole axial load is taken by the fasteners, then pretty much the bearing resistance is the leading design criteria, and I have to double the fasteners or the studs in many cases.
Thank you!
In advance, I want to say sorry for my English, especially for the technical expressions, they can be inaccurate sometimes.
Would you consider Bearing Resistance of the plate in a connection like the one below when we design the connection for axial load in the stud(Stud and Track of a light gauge steel residential structure) or we consider that the web of the stud and the track are connecting, and the axial load is transferred at the whole surface, not only at the fasteners? If I consider that the whole axial load is taken by the fasteners, then pretty much the bearing resistance is the leading design criteria, and I have to double the fasteners or the studs in many cases.
Thank you!
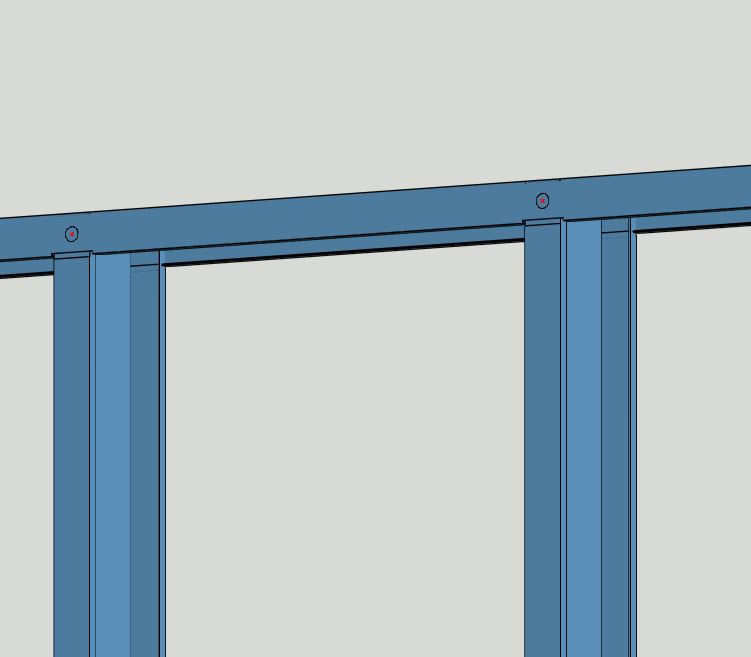