ElCidCampeador
Mechanical
Hi,
in an archive I've found a drawing of pressure vessel, design acc. to ASME VIII Div.1, where flanges are cladded as in the sketch here attached:
Flanges adopted were standard acc. to B16.5, mat. carbon steel, but raised face is completely removed (and also material from the inside body of the flange is removed) so that cladded layers are deposited on the surface to reach final dimension acc. to B16.5 and at the same time let cladding be enough for corrosion protection.
I know that in mechanical calculation, usually when there is cladding, this doesn't influence minimum thickness which is determined by carbon steel material.
But in this case, where part of carbon steel is removed from the body of flange and replaced by stainless steel? Is it necessary particular calculation, even if flange is standard?
Thank you
in an archive I've found a drawing of pressure vessel, design acc. to ASME VIII Div.1, where flanges are cladded as in the sketch here attached:
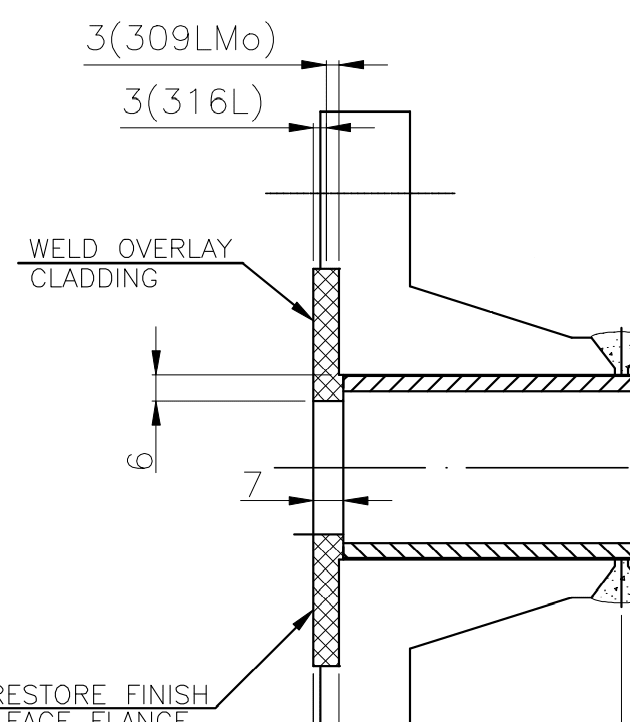
Flanges adopted were standard acc. to B16.5, mat. carbon steel, but raised face is completely removed (and also material from the inside body of the flange is removed) so that cladded layers are deposited on the surface to reach final dimension acc. to B16.5 and at the same time let cladding be enough for corrosion protection.
I know that in mechanical calculation, usually when there is cladding, this doesn't influence minimum thickness which is determined by carbon steel material.
But in this case, where part of carbon steel is removed from the body of flange and replaced by stainless steel? Is it necessary particular calculation, even if flange is standard?
Thank you