Hello!
Recently I have heard some steel fabricators say steel plates became warped
as they weld eight #8 rebars to 3/8"x8"x24"plate to make corbel plates for precast columns.
I did not hear this complaint before.
Is it due to poor welding skill?
Or, is it very hard to avoid warping problem?
Please let me know how I can avoid warping problem.
Thanks!
JRW
Recently I have heard some steel fabricators say steel plates became warped
as they weld eight #8 rebars to 3/8"x8"x24"plate to make corbel plates for precast columns.
I did not hear this complaint before.
Is it due to poor welding skill?
Or, is it very hard to avoid warping problem?
Please let me know how I can avoid warping problem.
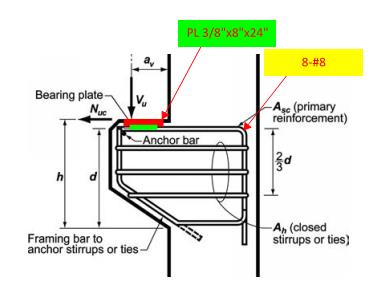
Thanks!
JRW