I'm pretty new here and still learning GD&T. In the imagine, I've seen both these GD&T call out recently. I was looking if anyone wants to walk me through this. To me I thought this would create redundancy and if there is a better way to go about this. I apologize in advice if this is a dumb question.
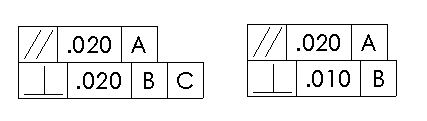