Hi,
I needed to evaluated the capacity of an angle with a concentrated load.
Bolts are in pairs each 12 inches and load can be either aligned with bolts, between bolts or any other position, but always in the same direction and high (3")
The proposed angle is L6x6x1/2, but I have modeled it as areas in SAP2000 and stresses are higher than Fy/1.67 for bending.
Is the thickness not enough? How can I evaluate it better?
I needed to evaluated the capacity of an angle with a concentrated load.
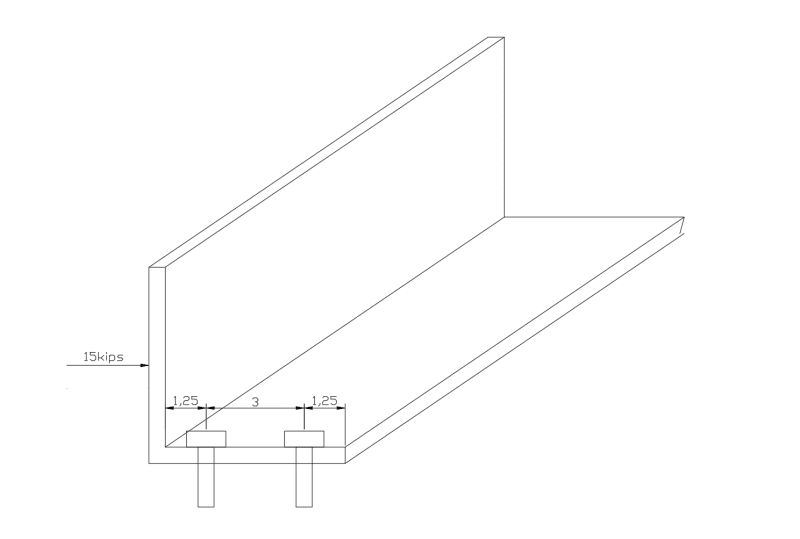
Bolts are in pairs each 12 inches and load can be either aligned with bolts, between bolts or any other position, but always in the same direction and high (3")
The proposed angle is L6x6x1/2, but I have modeled it as areas in SAP2000 and stresses are higher than Fy/1.67 for bending.
Is the thickness not enough? How can I evaluate it better?