milkshakelake
Structural
I have two 8x36 "wallumns" next to two 12x24 columns. The FEM results show a massive overstress in punching shear due to the minor axis moment.
Can I pin these columns to remove the moment? Normally, I don't do this because it's very unconservative for punching shear. But my engineering gut is telling me that these wallumns are almost like shear walls, where I do release the moment. So if it works for shear walls, it should work for this. Visually and intuitively, they're taking quite small loads. But I don't want it to actually punch through in real life, especially when the overstress is this high.
That being said, I'd also like to check this by hand. I think my go-to, the direct design method, is out the window because it doesn't meet the conditions. Can someone guide me in the right direction for doing a secondary check?
The other option is to just remove these columns, but I don't like it. It's a 6' cantilever with heavy SDL (concrete pavers).
Can I pin these columns to remove the moment? Normally, I don't do this because it's very unconservative for punching shear. But my engineering gut is telling me that these wallumns are almost like shear walls, where I do release the moment. So if it works for shear walls, it should work for this. Visually and intuitively, they're taking quite small loads. But I don't want it to actually punch through in real life, especially when the overstress is this high.
That being said, I'd also like to check this by hand. I think my go-to, the direct design method, is out the window because it doesn't meet the conditions. Can someone guide me in the right direction for doing a secondary check?
The other option is to just remove these columns, but I don't like it. It's a 6' cantilever with heavy SDL (concrete pavers).
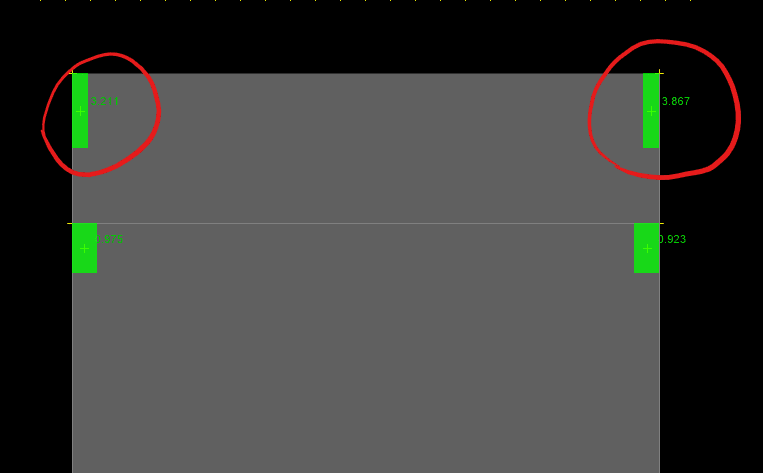