Please refer to my sketches below.
I have a handrail post that will bolt onto a baseplate, which is welded to a square hollow section.
I am wondering what the typical process of fabricating this would be? Will the baseplate be holed and tapped before welding onto the SHS, or welded first and then holed and tapped?
If the former, I suppose I would just allow for some holes in the top of the SHS to allow the bolts to pass through, perhaps ~20 or 24 diameter.
If the latter, is there any issue with tapping through two separate pieces of steel?
Note that the 25 thick plate alone provides enough thread engagement in this case, so I am not relying on any additional thread in the SHS.
I have a handrail post that will bolt onto a baseplate, which is welded to a square hollow section.
I am wondering what the typical process of fabricating this would be? Will the baseplate be holed and tapped before welding onto the SHS, or welded first and then holed and tapped?
If the former, I suppose I would just allow for some holes in the top of the SHS to allow the bolts to pass through, perhaps ~20 or 24 diameter.
If the latter, is there any issue with tapping through two separate pieces of steel?
Note that the 25 thick plate alone provides enough thread engagement in this case, so I am not relying on any additional thread in the SHS.
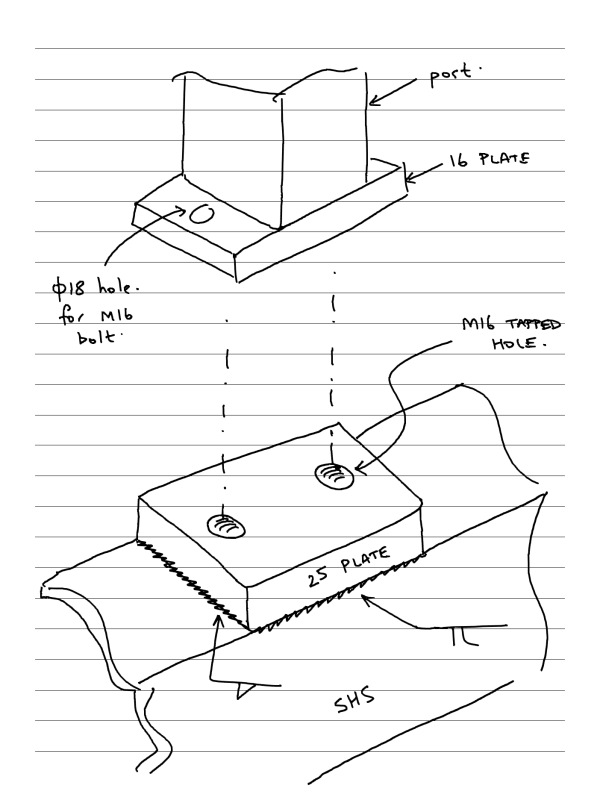
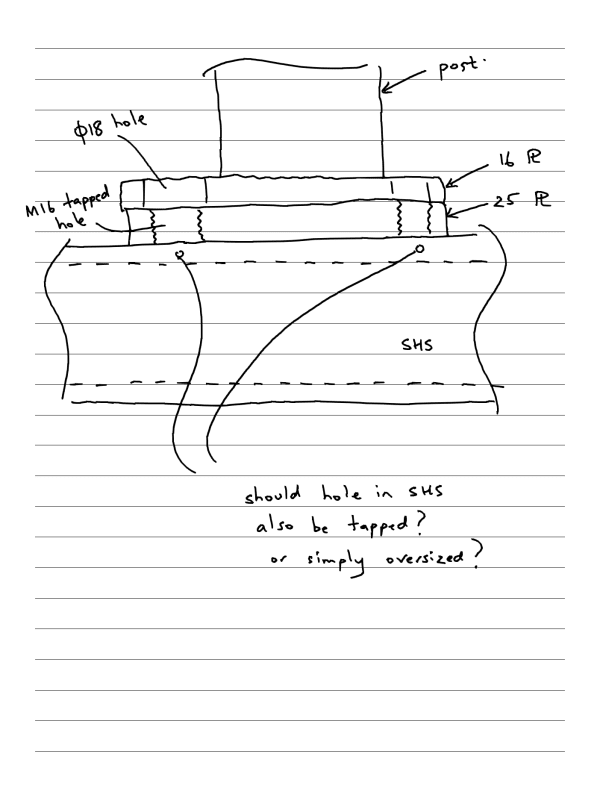