nivoo_boss
Structural
Hey everyone!
So I have this rather long (~100 m) two-storey building. It's supported by RC columns. The second floor is made up of RC beams and hollow core slabs. The roof has steel trusses. The columns are spaced 6 m and 12 m. It has a masonry wall running in the middle across the building.
The plan is shaped like a trapezoid. I want to use the hollow core floor as a diaphragm to transfer the wind loads to the surrounding walls I marked on the plans. Perhaps you can give some advice on how to analyze this diaphragm reasonably? On the side and gable walls I would use steel bracings and in the middle there is a masonry wall. There is no seismic activity in my region.
1) A general plan of the diaphragm:
2) A plan with the slabs, columns etc:
3) A section and a diagram. I would like to use this diagram to design the columns:
So I have this rather long (~100 m) two-storey building. It's supported by RC columns. The second floor is made up of RC beams and hollow core slabs. The roof has steel trusses. The columns are spaced 6 m and 12 m. It has a masonry wall running in the middle across the building.
The plan is shaped like a trapezoid. I want to use the hollow core floor as a diaphragm to transfer the wind loads to the surrounding walls I marked on the plans. Perhaps you can give some advice on how to analyze this diaphragm reasonably? On the side and gable walls I would use steel bracings and in the middle there is a masonry wall. There is no seismic activity in my region.
1) A general plan of the diaphragm:
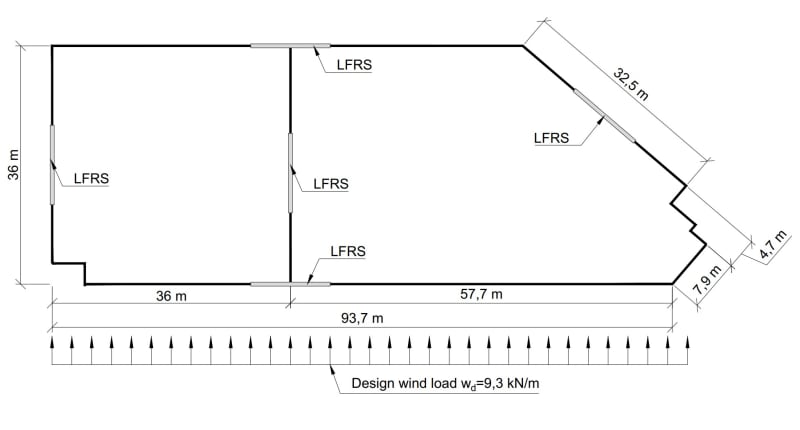
2) A plan with the slabs, columns etc:
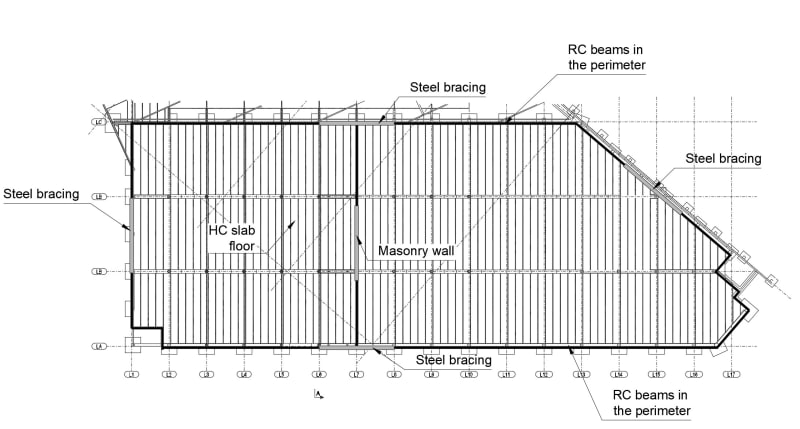
3) A section and a diagram. I would like to use this diagram to design the columns:
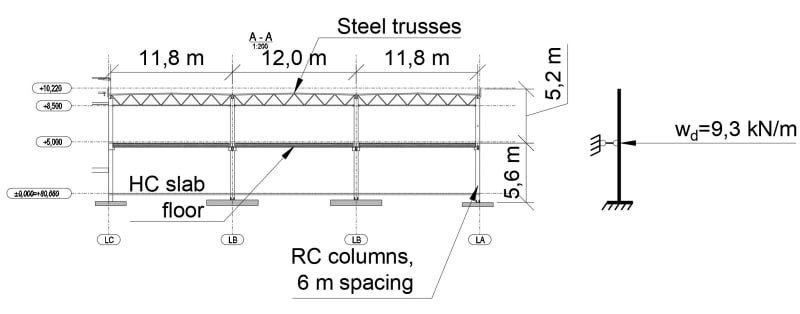