Pavan Kumar
Chemical
Hi All,
I am trying to calculate the Steam condensate load for a low pressure steam line inlet to the control valve that feeds steam to the Steam bundle of the butane vaporizer ( please see sketch pasted below). This is to check the adequacy of the existing 1/2" TLV Free float steam trap. The trap has a capacity of 300 lb/hr at our operating conditions.
The inlet line to the control valve is 3" Sch 40 CS pipe that is 85 feet long with many bends in it. It is insulated with 2" thick mineral wool insulation. There is a 1/2" TLV SS3V-18 free float steam trap on the inlet line(see sketch). The LP steam is let down from the regulator from 265 psig to 70 psig. Due iso-enthalpic expansion the steam superheats and the temperature at the regulator outlet is 175.826 Deg C at 70 psig pressure(with 18.06 Deg C degree of superheat). The steam flow rate is 2660.6 lb/hr. I assumed the steam temperature to be constant at 175.826 Deg C through the entire line and calculated the heat loss through the pipe and insulation by considering
(i) resistance of the pipe wall ( very minimal)
(ii) resistance of insulation.
(iii) resistance of ambient air to remove the heat. Assumed the ambient air at 70 Deg F.
I used the following formulae for the heat flow through pipe, insulation and to the ambient air
where D1, D2 and D3 are the pipe ID, OD and OD of the insulation respectively
T1 , T2 and T3 are the temperatures at pipe inside surface, outside surface and the outside surface of the insulation
R1, R2, and R3 are the resistances of the pipe wall, insulation and ambient air respectively.
After a few iterations I was able to calculate the heat loss to qLoss = 7935.2 lb/hr. The calculation spreadsheet is attached with this post.
The specific enthalpy of superheated steam at 70 psig and 175.826 Deg C is 1202.748 Btu/lb . With flow rate of 2660.6 lb/hr the heat load of steam is 2660.6*1202.748 = 3200019 Btu/hr. Subtracting the pipe heat loss of 7935.2 Btu/hr dividing the result with the steam flow rate the specific enthalpy of steam at the control valve inlet is 1199.8 Btu/lb.
There is a pressure drop of 13.52 psi in the inlet line to the control valve. So the pressure at the control valve inlet is 56.48 psig. Checking the steam condition with P= 56.48 psig and specific enthalpy of 1199.8 Btu/lb in the steam tables, I find that the steam condition is still superheated with a temperature of 169.9 Deg C with a degree of superheat of 18.8 Deg C. This means that there should not be any condensation. But we do see condensate coming out of the tarp in operation. I can see the condensate as the trap is leaking right now. This means my calculation is not correct. I want to correct my calculation and hence this post. I request your help in this regard.
Thanks and Regards,
Pavan Kumar
I am trying to calculate the Steam condensate load for a low pressure steam line inlet to the control valve that feeds steam to the Steam bundle of the butane vaporizer ( please see sketch pasted below). This is to check the adequacy of the existing 1/2" TLV Free float steam trap. The trap has a capacity of 300 lb/hr at our operating conditions.
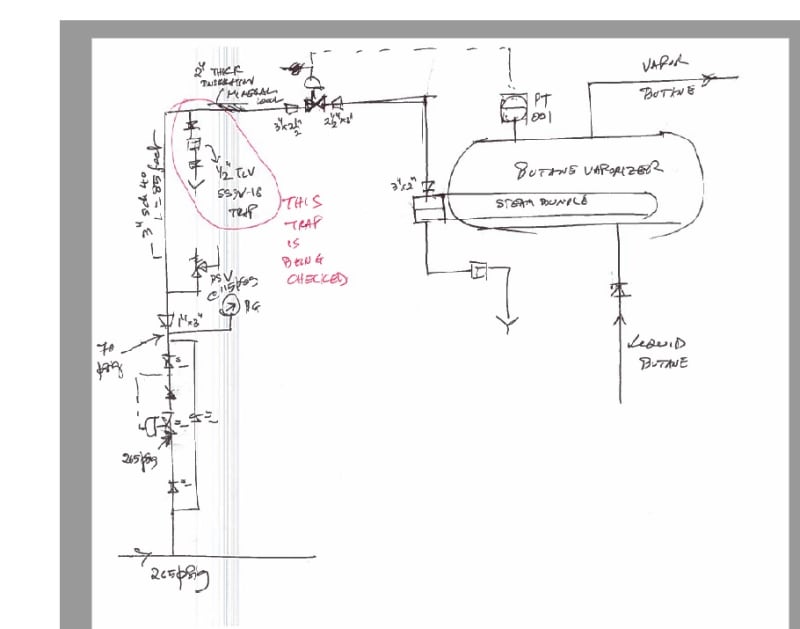
The inlet line to the control valve is 3" Sch 40 CS pipe that is 85 feet long with many bends in it. It is insulated with 2" thick mineral wool insulation. There is a 1/2" TLV SS3V-18 free float steam trap on the inlet line(see sketch). The LP steam is let down from the regulator from 265 psig to 70 psig. Due iso-enthalpic expansion the steam superheats and the temperature at the regulator outlet is 175.826 Deg C at 70 psig pressure(with 18.06 Deg C degree of superheat). The steam flow rate is 2660.6 lb/hr. I assumed the steam temperature to be constant at 175.826 Deg C through the entire line and calculated the heat loss through the pipe and insulation by considering
(i) resistance of the pipe wall ( very minimal)
(ii) resistance of insulation.
(iii) resistance of ambient air to remove the heat. Assumed the ambient air at 70 Deg F.
I used the following formulae for the heat flow through pipe, insulation and to the ambient air
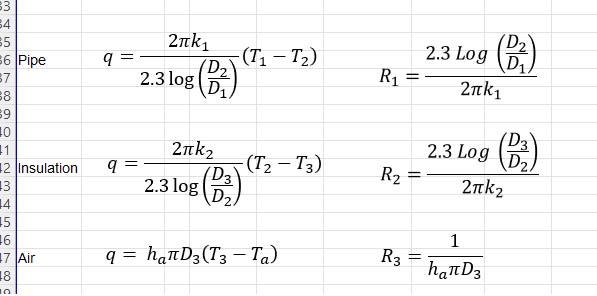
where D1, D2 and D3 are the pipe ID, OD and OD of the insulation respectively
T1 , T2 and T3 are the temperatures at pipe inside surface, outside surface and the outside surface of the insulation
R1, R2, and R3 are the resistances of the pipe wall, insulation and ambient air respectively.
After a few iterations I was able to calculate the heat loss to qLoss = 7935.2 lb/hr. The calculation spreadsheet is attached with this post.
The specific enthalpy of superheated steam at 70 psig and 175.826 Deg C is 1202.748 Btu/lb . With flow rate of 2660.6 lb/hr the heat load of steam is 2660.6*1202.748 = 3200019 Btu/hr. Subtracting the pipe heat loss of 7935.2 Btu/hr dividing the result with the steam flow rate the specific enthalpy of steam at the control valve inlet is 1199.8 Btu/lb.
There is a pressure drop of 13.52 psi in the inlet line to the control valve. So the pressure at the control valve inlet is 56.48 psig. Checking the steam condition with P= 56.48 psig and specific enthalpy of 1199.8 Btu/lb in the steam tables, I find that the steam condition is still superheated with a temperature of 169.9 Deg C with a degree of superheat of 18.8 Deg C. This means that there should not be any condensation. But we do see condensate coming out of the tarp in operation. I can see the condensate as the trap is leaking right now. This means my calculation is not correct. I want to correct my calculation and hence this post. I request your help in this regard.
Thanks and Regards,
Pavan Kumar