hirschaplin
Petroleum
Hello,
I am looking to make rotors in accordance with API 619.
As per guiding table F.1 in Annex F, they are suggesting the following materials to choose from:
Shaft
Rotor body
I understand that the listed materials are not mandatory for code compliance but recommended based on experience and best practices. With that said I am a bit surprised to not see AISI 4140 steel listed as this seems to be a very popular material in demanding rotor/shaft applications, any idea why it is excluded? However I would feel that the selection of another material than any of the ones listed would yield a deviation in our API 619 deviations list and that should be avoided unless strictly necessary.
Our design is consisting of a solid rotor with integral shafts. Meaning that the rotor body and shaft is not separated parts - they are one and same!
I am thinking about AISI 1045 (highlighted above) as the best standard material for us as it is suggested for both shaft and rotor body as well as it allows for a great temperature range while being acceptable for both DS and OF compressors.
I am a bit confused about AISI 1045 as a standard material as I understand it origins out of ASTM A29. But ASTM A29 is not providing detailed guidance as it more seems to be a standard with general requirements for various steel bars as it says in the scope text:
API 619 clearly states that 1045 shall be forged but it seems like the common supply of this material is hot-rolled or cold drawn even though some information I found on Google indicates that forging is possible as well but then what is the ASTM standard that apply for AISI 1045 custom forgings?
Preferably the best solution for us would be if the rotor could be machined out of a round or flat bar, but then I understand that this is not a proper forging and you run into this kind of problem in the material structure:
Micro structure of a bar
Micro structure of a machined bar
Micro structure of proper forging
Is this understanding correct? Meaning that we can't machine our rotor out of a solid hot-rolled or cold drawn bar? Even if the bar was properly forged I understand that we can't create the rotor out of the bar to benefit from the proper forging process? If this is correct, then I guess that the proper rotor raw forging must look very must similar to the final shape of the rotor? For example the final dimensions +3 mm or whatever tolerance that is needed to machine the rotor clean? Is it even possible to forge such a screw rotor?
Or what is the meaning of "AISI 1045 forged" in this context, what would satisfy the standard as well as the demanding customers of such compressor?
I need compliance with NACE MR0103 and NACE MR0175. I know typically that NACE MR0175 requires a hardness test for various carbon steel materials with a result of not more than 22 HRC. But this is not the only requirement I guess? What properties and limits are needed for AISI 1045 to declare compliance with NACE MR0103 and NACE MR0175?
ASTM A29 doesn't provide any information about elevated or room temperature tensile properties and it doesn't provide any acceptable impact properties at low temperature (-29 deg C). Is it defined within the ASME code or where can I find this information?
Finally what about heat treatment? The API 619 specifies the following "Only fully killed or normalized steels made to fine-grain practice shall be used", shall I go with Normalizing, Annealing or Quenching & Tempering(QT) to satisfy all of the above?
I can't run stress simulations until this is figured out as I need relevant strength values before we run our simulations.
Thank you!
I am looking to make rotors in accordance with API 619.
As per guiding table F.1 in Annex F, they are suggesting the following materials to choose from:
Shaft
Code:
Material Specification Oil-Flooded, Dry-Screw Form °C Min. °C Max. °F Min. °F Max.
Ductile iron JIS G 5502 FCD700 OF Cast – 29 350 – 20 662
Steel AISI 1030-1035 OF Forged – 29 399 – 20 750
[highlight #FCE94F]Steel AISI 1040-1050 OF & DS Forged – 29 343 – 20 650 [/highlight]
Steel ASTM A350 LF2 OF Forged – 45 – 49
Steel ASTM A668 class D - 1030 DS Forged – 29 399 – 20 750
Steel EN 10083 25 CrMo4 DS Forged – 10 300 14 572
Steel EN 10083 C45N OF Forged – 29 399 – 20 750
Steel JIS G 4051 S30C OF & DS Forged – 10 450 14 842
Steel JIS G 4051 S45C OF Forged – 10 450 14 842
Steel JIS G 4051 S55C OF Forged – 10 450 14 842
Steel JIS G 4105 SCM430 DS Forged – 30 400 – 22 752
Steel SAE1137 OF Forged — — — —
Stainless steel ASTM A473 type 304L DS Forged – 196 400 – 321 752
Stainless steel ASTM A473 type 316L DS Forged – 196 400 – 321 752
Stainless steel ASTM A479 class 1 Type 410 DS Bar – 59 345 – 75 650
Stainless steel EN 10088 X3CrNiMo 13-4 DS Forged – 105 300 – 157 572
Stainless steel EN 10088 (all parts) X17CrNi16-2DS Forged — — — —
Stainless steel JIS G 3214 SUS F 6NM/13Cr-4Ni DS Forged – 105 300 – 157 752
Stainless steel JIS G 3214 SUS304 DS Forged – 196 400 – 321 752
Stainless steel JIS G 3214 SUS316 DS Forged – 196 400 – 321 752
Stainless steel JIS G 3214 SUS405 DS Forged – 10 400 14 752
Rotor body
Code:
Material Specification Oil-Flooded, Dry-Screw Form °C Min. °C Max. °F Min. °F Max.
Ductile iron JIS G 5502 FCD600 OF Cast – 29 260 – 20 500
Ductile iron JIS G 5502 FCD700 OF Cast – 29 350 – 20 662
[highlight #FCE94F]Steel AISI 1030-1045 OF & DS Forged – 29 399 – 20 750 [/highlight]
Steel ASTM A350 LF2 OF Forged – 45 149 – 49 300
Steel ASTM A668 class D - 1030 DS Forged – 29 399 – 20 750
Steel EN 10083 (all parts) 25CrMo 4 DS Forged – 10 300 14 572
Steel EN 10083 (all parts) C45N OF Forged – 29 399 – 20 750
Steel JIS G 3221 SFCM 930S OF Forged – 29 399 – 20 750
Steel JIS G 4051 S30C OF & DS Forged – 10 450 14 842
Steel JIS G 4051 S45C OF Forged – 10 450 14 842
Steel JIS G 4051 S55C OF Forged – 10 450 14 842
Steel JIS G 4105 SCM430 OF Forged – 30 400 – 22 752
Steel SAE1137 OF Forged — — — —
Stainless steel ASTM A473 type 431 DS Forged — — — —
Stainless steel ASTM A473 type 304L DS Forged – 196 400 – 321 752
Stainless steel ASTM A473 type 316L DS Forged – 196 400 – 321 752
Stainless steel ASTM A479 class 1 Type 410 DS Bar – 59 345 – 75 650
Stainless steel EN 10088 X3CrNiMo 13-4 DS Forged – 105 300 – 157 572
Stainless steel JIS G 3214 SUS 405 DS Forged – 10 400 14 752
Stainless steel JIS G 3214 SUS F 6NM/13Cr-4Ni DS Forged – 105 300 – 157 572
Stainless steel JIS G 3214 SUS304 DS Forged – 196 400 – 321 752
Stainless steel JIS G 3214 SUS316 DS Forged – 196 400 – 321 752
I understand that the listed materials are not mandatory for code compliance but recommended based on experience and best practices. With that said I am a bit surprised to not see AISI 4140 steel listed as this seems to be a very popular material in demanding rotor/shaft applications, any idea why it is excluded? However I would feel that the selection of another material than any of the ones listed would yield a deviation in our API 619 deviations list and that should be avoided unless strictly necessary.
Our design is consisting of a solid rotor with integral shafts. Meaning that the rotor body and shaft is not separated parts - they are one and same!
I am thinking about AISI 1045 (highlighted above) as the best standard material for us as it is suggested for both shaft and rotor body as well as it allows for a great temperature range while being acceptable for both DS and OF compressors.
I am a bit confused about AISI 1045 as a standard material as I understand it origins out of ASTM A29. But ASTM A29 is not providing detailed guidance as it more seems to be a standard with general requirements for various steel bars as it says in the scope text:
A29/A29M – 12 said:"1. Scope
1.1 This specification2 covers a group of common requirements
which, unless otherwise specified in the purchase order
or in an individual specification, shall apply to carbon and alloy
steel bars under each of the following ASTM specifications (or
under any other ASTM specification which invokes this
specification or portions thereof): [...]"
API 619 clearly states that 1045 shall be forged but it seems like the common supply of this material is hot-rolled or cold drawn even though some information I found on Google indicates that forging is possible as well but then what is the ASTM standard that apply for AISI 1045 custom forgings?
Preferably the best solution for us would be if the rotor could be machined out of a round or flat bar, but then I understand that this is not a proper forging and you run into this kind of problem in the material structure:
Micro structure of a bar
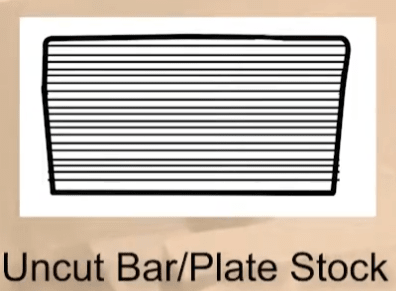
Micro structure of a machined bar
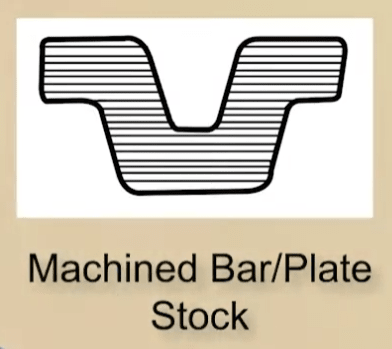
Micro structure of proper forging
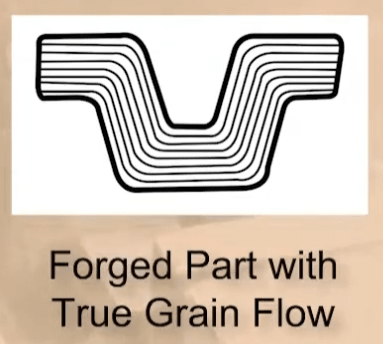
Is this understanding correct? Meaning that we can't machine our rotor out of a solid hot-rolled or cold drawn bar? Even if the bar was properly forged I understand that we can't create the rotor out of the bar to benefit from the proper forging process? If this is correct, then I guess that the proper rotor raw forging must look very must similar to the final shape of the rotor? For example the final dimensions +3 mm or whatever tolerance that is needed to machine the rotor clean? Is it even possible to forge such a screw rotor?
Or what is the meaning of "AISI 1045 forged" in this context, what would satisfy the standard as well as the demanding customers of such compressor?
I need compliance with NACE MR0103 and NACE MR0175. I know typically that NACE MR0175 requires a hardness test for various carbon steel materials with a result of not more than 22 HRC. But this is not the only requirement I guess? What properties and limits are needed for AISI 1045 to declare compliance with NACE MR0103 and NACE MR0175?
ASTM A29 doesn't provide any information about elevated or room temperature tensile properties and it doesn't provide any acceptable impact properties at low temperature (-29 deg C). Is it defined within the ASME code or where can I find this information?
Finally what about heat treatment? The API 619 specifies the following "Only fully killed or normalized steels made to fine-grain practice shall be used", shall I go with Normalizing, Annealing or Quenching & Tempering(QT) to satisfy all of the above?
I can't run stress simulations until this is figured out as I need relevant strength values before we run our simulations.
Thank you!