NeedanewGC
Structural
- Jun 26, 2023
- 2
I recently was reviewing photographs of a structure that was constructed and became aware that the general contactor intentionally poured a cold joint in the monolithic slab foundation for a metal building. The project is located in a high velocity wind zone and the thickened edge of the mono slab was designed to be 24" deep and 9' wide with anchor bolts for the metal building columns at 20' centers. Building is 100' x 80'. The pictures I reviewed were clear that the first 16" of the bottom of the slabs "thickened edge foundation" was poured on one date and then 3 weeks later the the slab was then poured on top of the perimeter foundation. The anchor bolts were supposed to have been embedded 12". The top bar was not placed at the proposed height of the thickened edge. Instead the contractor pushed the rebar down to allow his unnecesary form create a vertical edge, 4.5" below the proposed top of the thickened edge foundation.
The job is nearing completion and the owner is not understanding of the impact of this. I am not the engineer of record, but cannot ignore this. Any thoughts ?
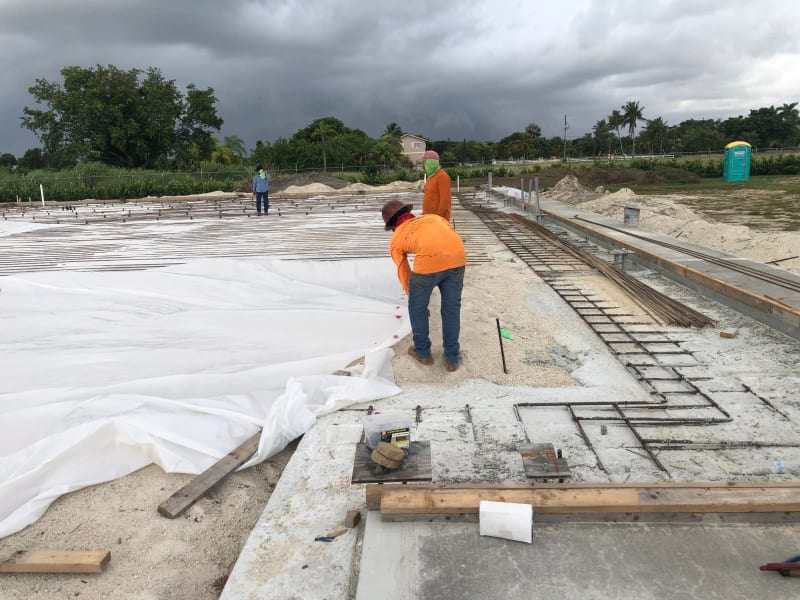
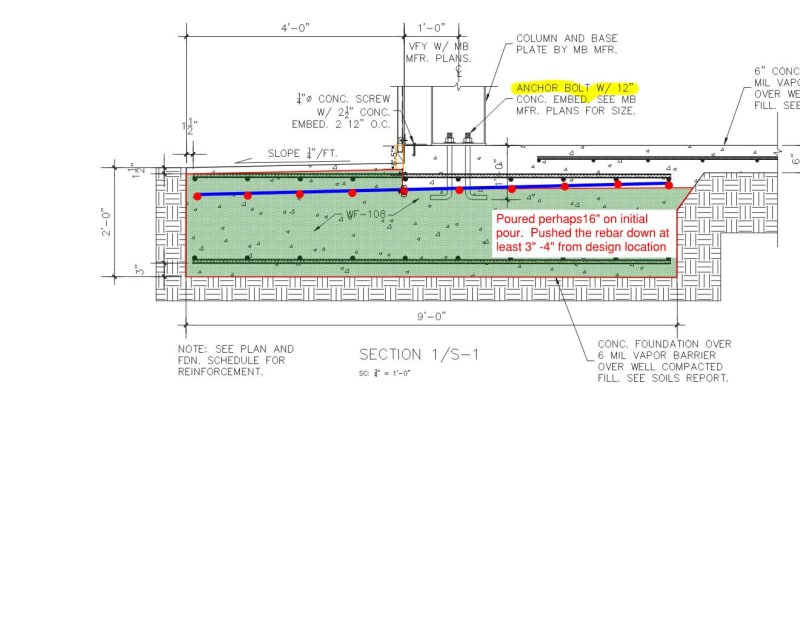