Vivaldi M. Smith
Chemical
- Feb 16, 2022
- 59
Good morning.
I am trying to design two flow orifices to be able to reduce the DP to protect downstream pressure ( Closed Drain). The pressure in the line is around 1100 PSIG, one line is gas, and the other line is liquid.
The Gas line ( natural gas ) is 12" and the distance from valve to valve is about 41 feet. The liquid line ( Condensate) is 6" about the same distance, 41 feet. If I calculate the volume trap in the pipe, how do I find the time to depressurize through a 2-inch completely? it is that flow that I want to use to calculate the flow orifice. will that be correct?
Please help.
I am trying to design two flow orifices to be able to reduce the DP to protect downstream pressure ( Closed Drain). The pressure in the line is around 1100 PSIG, one line is gas, and the other line is liquid.
The Gas line ( natural gas ) is 12" and the distance from valve to valve is about 41 feet. The liquid line ( Condensate) is 6" about the same distance, 41 feet. If I calculate the volume trap in the pipe, how do I find the time to depressurize through a 2-inch completely? it is that flow that I want to use to calculate the flow orifice. will that be correct?
Please help.
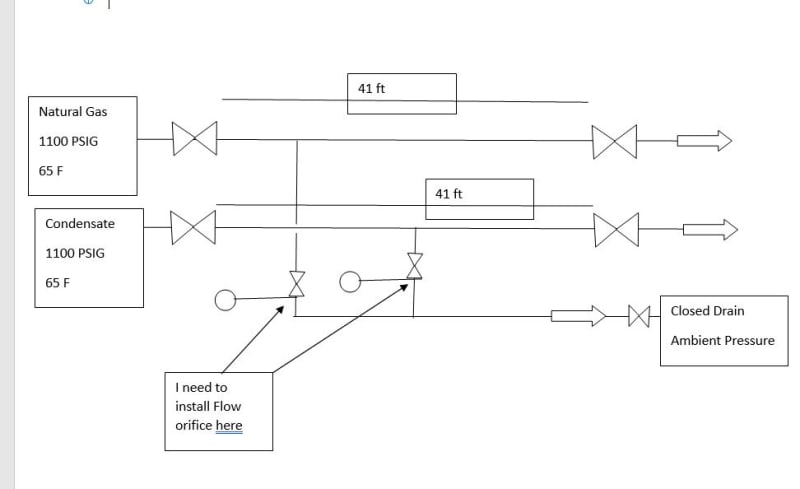