Struct2Mech
Civil/Environmental
Hi,
I'm looking to use a through-bolt to join two steel angle sections to an aluminum SHS (as pictured).
The bolt will be subject to both shear and tension (some prying) and largely dynamic loads (vibration and impact). The bolt will also only likely be snug tight (reliant on a layman to tighten the bolt with hand tools).
I'm struggling to know how to check the connection for strength. For snug tight through-bolts in HSS subject to mostly static loads, a bolt should be treated as a pin. As this isn't a static load, I'm unsure how to proceed and I'm struggling to find any relevant literature.
I'm also concerned about the bolts loosening and I'd appreciate any referrals to text that might help me there too.
Can anyone point me in the right direction?
Thanks heaps!
I'm looking to use a through-bolt to join two steel angle sections to an aluminum SHS (as pictured).
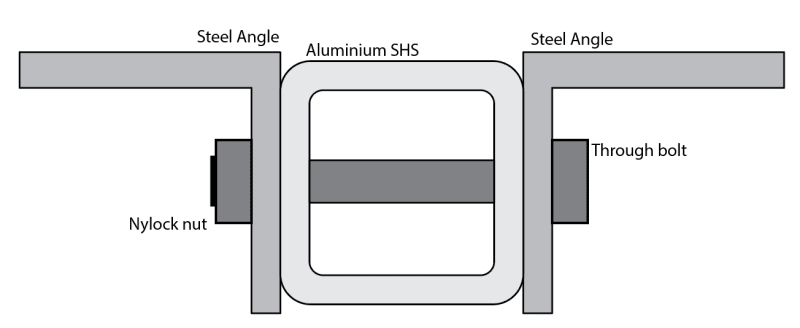
The bolt will be subject to both shear and tension (some prying) and largely dynamic loads (vibration and impact). The bolt will also only likely be snug tight (reliant on a layman to tighten the bolt with hand tools).
I'm struggling to know how to check the connection for strength. For snug tight through-bolts in HSS subject to mostly static loads, a bolt should be treated as a pin. As this isn't a static load, I'm unsure how to proceed and I'm struggling to find any relevant literature.
I'm also concerned about the bolts loosening and I'd appreciate any referrals to text that might help me there too.
Can anyone point me in the right direction?
Thanks heaps!