hdb35
Structural
- Sep 18, 2023
- 4
Hello, I have several questions about a connection I am designing.
The building is a one story CMU (10m x 30m x 4.5m high) with steel roof trusses made from SHS Sections.
The steel trusses are modeled as simply supported, and the connection I am specifying is to weld the bottom truss chord to a base plate that sits on top of the masonry walls, and is connected by 2 - cast in plate headed anchor bolts. I am also specifying slotted connections on one side to simulate the "roller" connection. (See detail)
To design the anchor bolts for tension, I got the maximum uplift reaction at a single truss location subjected to components and cladding forces in a 3D model. This came out to around 22KN or 5 kips of uplift (each bolt is designed for 2.5kips in tension).
However, when designing the bolts for shear, I am unsure what forces to design the bolts for? This masonry building has designated "shear walls" at the four corners in both directions, so ideally I would think the a lateral wind load would travel through the roof diaphragm (the metal sheeting) and transfer to the shear walls. How do we account for this transfer or force?
In a 3D model with the MWFRS wind loads applied to the truss, I see a max lateral force at one connection as 30 KN, or 6.7 Kips - this would cause the anchor bolts to fail in shear considerably. I do not think in reality this much lateral force would be on the truss connections but instead most of it would transfer to the shear walls?
Also the end walls of the structure in the short direction are masonry gable walls - so any advice on how to connect the end purlins to these end walls would be appreciated as well to ensure a desired load path to shear walls? (Ie rake beam details or etc).
Again, I am not sure how lateral load is transferred from the roof diaphragm to the shear walls. If there is anything I am missing or misunderstanding here I would love to hear anyone's thoughts.
The building is a one story CMU (10m x 30m x 4.5m high) with steel roof trusses made from SHS Sections.
The steel trusses are modeled as simply supported, and the connection I am specifying is to weld the bottom truss chord to a base plate that sits on top of the masonry walls, and is connected by 2 - cast in plate headed anchor bolts. I am also specifying slotted connections on one side to simulate the "roller" connection. (See detail)
To design the anchor bolts for tension, I got the maximum uplift reaction at a single truss location subjected to components and cladding forces in a 3D model. This came out to around 22KN or 5 kips of uplift (each bolt is designed for 2.5kips in tension).
However, when designing the bolts for shear, I am unsure what forces to design the bolts for? This masonry building has designated "shear walls" at the four corners in both directions, so ideally I would think the a lateral wind load would travel through the roof diaphragm (the metal sheeting) and transfer to the shear walls. How do we account for this transfer or force?
In a 3D model with the MWFRS wind loads applied to the truss, I see a max lateral force at one connection as 30 KN, or 6.7 Kips - this would cause the anchor bolts to fail in shear considerably. I do not think in reality this much lateral force would be on the truss connections but instead most of it would transfer to the shear walls?
Also the end walls of the structure in the short direction are masonry gable walls - so any advice on how to connect the end purlins to these end walls would be appreciated as well to ensure a desired load path to shear walls? (Ie rake beam details or etc).
Again, I am not sure how lateral load is transferred from the roof diaphragm to the shear walls. If there is anything I am missing or misunderstanding here I would love to hear anyone's thoughts.
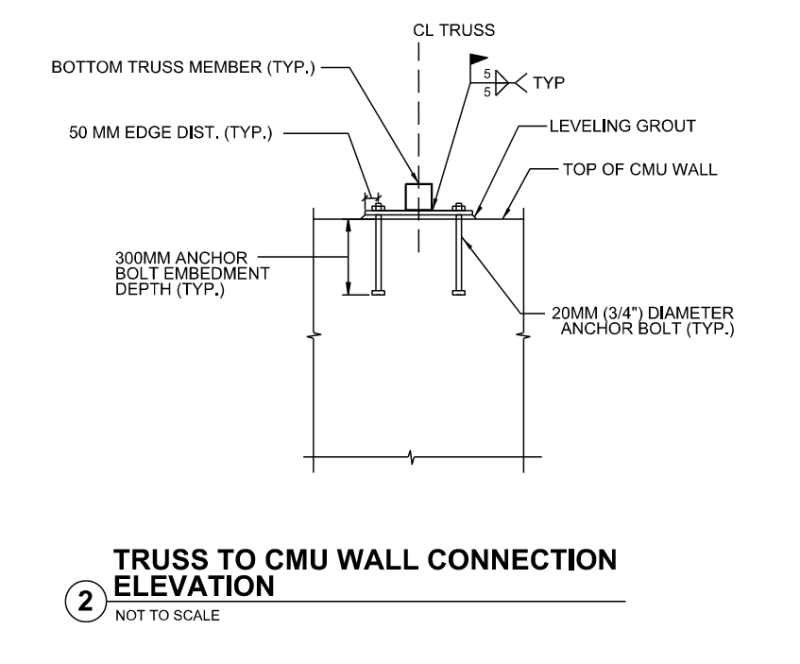
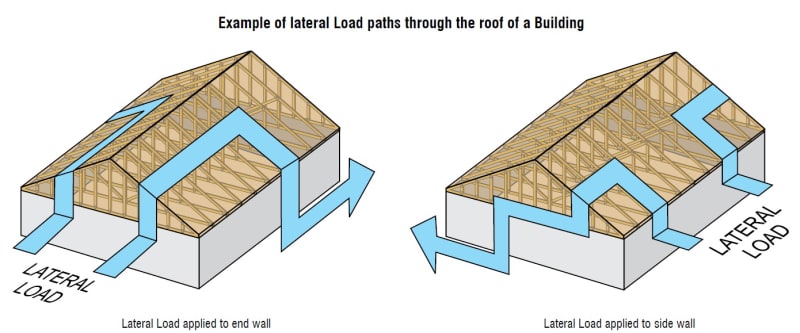