rollingcloud
Aerospace
- Aug 9, 2022
- 171
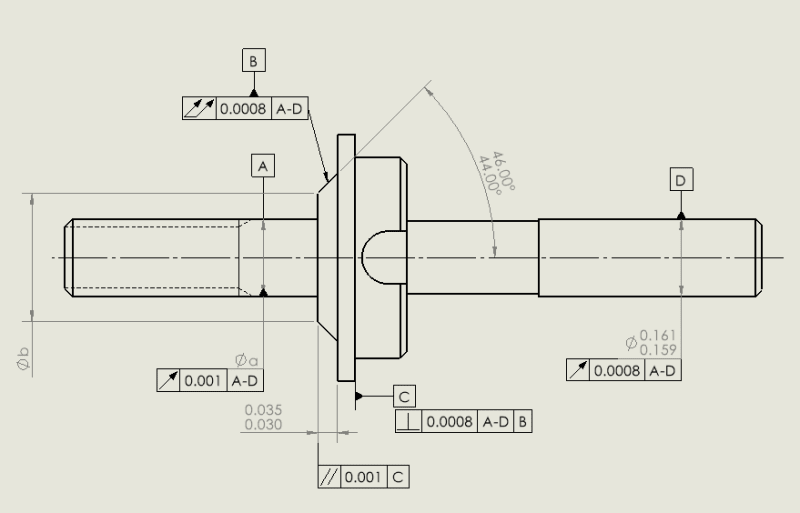
The function of the rod is to provide a platform (datum C) for a spring and a sealing surface (datum B), when pressure is too high, the rod moves to the right.
My main concern is the feasibility of the total runout over short distance. (Datum D is not critical, guided by a bushing to prevent too much misalignment.)