I have a small two storey bldg I am working on. The roof diaphragm is a flexible steel deck over OWSJ as you can see in the image below. My question relates to the one drag strut. I have seen a channel section used commonly for this purpose. The flanges are cut out at the OWSJ and it is welded to the OWSJ top chords. I have seen it in the field and I am not a fan of the effect it has on the decking in this area. What are others doing here?
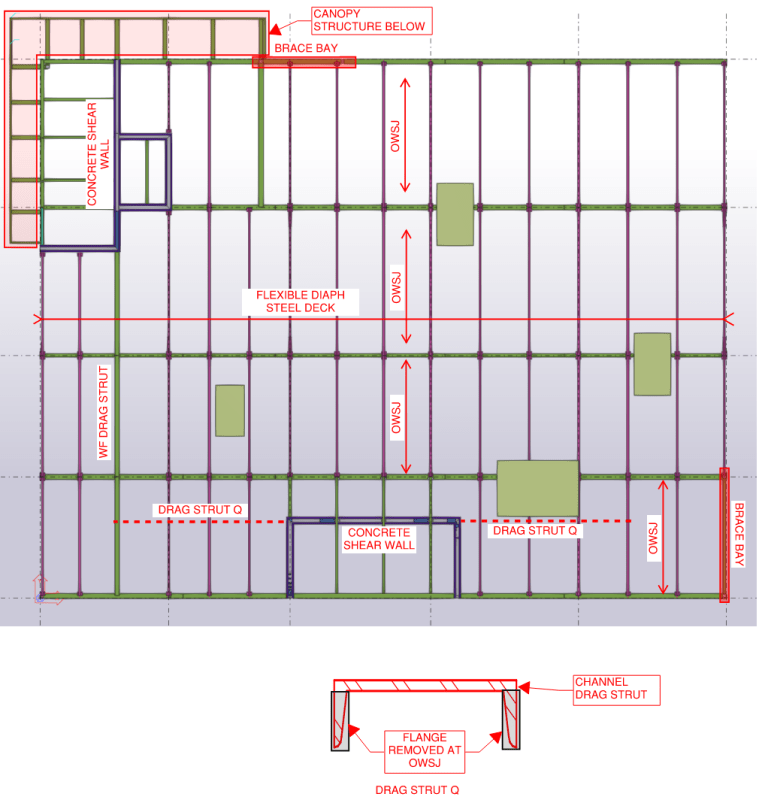