hi, all,
this is a question related to corrosion of SS under high temperature ammonia gas.
It's the AIG(Ammonia Injection Grid)in the Boiler system, which funcitons to control the NOx in flue gas by injecting gaseous ammonia of a high temperature around 400C.
the Ammonia distributing pipe are fabricated with 304, while i find the follow table in a corrosion handbook:
it implies that 304 is not compatible to the temperature higher than 90F(32C), under which condition the corrosion rate is larger than 20 mpy, while in other sources, like NICKLE INSTITUTE states that "the stainless steels are used safely for high-temperature service in hot ammonia atmospheres". i believe both the sources, ther must be something wrong with my understanding, could you please shed some light on it? also, what is the corrosion mechanism of Ammonia in high temperature?
Thanks so much.
this is a question related to corrosion of SS under high temperature ammonia gas.
It's the AIG(Ammonia Injection Grid)in the Boiler system, which funcitons to control the NOx in flue gas by injecting gaseous ammonia of a high temperature around 400C.
the Ammonia distributing pipe are fabricated with 304, while i find the follow table in a corrosion handbook:
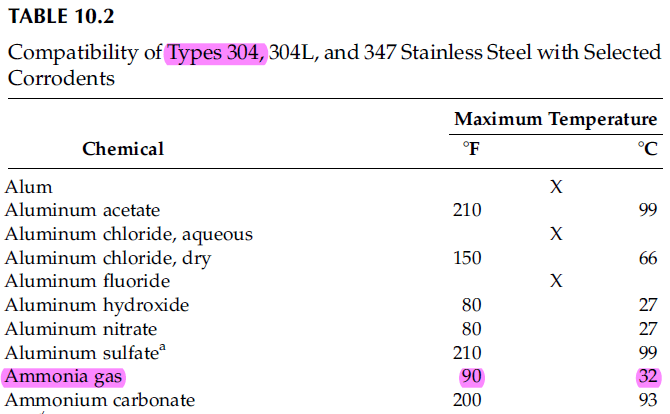
it implies that 304 is not compatible to the temperature higher than 90F(32C), under which condition the corrosion rate is larger than 20 mpy, while in other sources, like NICKLE INSTITUTE states that "the stainless steels are used safely for high-temperature service in hot ammonia atmospheres". i believe both the sources, ther must be something wrong with my understanding, could you please shed some light on it? also, what is the corrosion mechanism of Ammonia in high temperature?
Thanks so much.