Stefan2211
Chemical
- Jun 25, 2020
- 104
Dear All,
our contractor looks for a common way how to weld a 3/4" pipe (304) into a 3/4 "sockolet (304). The gap between sockolet and inserted pipe is to small (~0.1mm) to purge the oxygen completely with forming gas. There will be a risk of crevice corrosion. The pipe (3") uses many sockolets so it is not possiple to purge from the 3" pipe due to all the holes of the sockolets. It is very time consuming.
Any practical solution like drilling a small hole on the side of the sockolet to easier purge?
I guess there is a common used way to do it.
Thanks
our contractor looks for a common way how to weld a 3/4" pipe (304) into a 3/4 "sockolet (304). The gap between sockolet and inserted pipe is to small (~0.1mm) to purge the oxygen completely with forming gas. There will be a risk of crevice corrosion. The pipe (3") uses many sockolets so it is not possiple to purge from the 3" pipe due to all the holes of the sockolets. It is very time consuming.
Any practical solution like drilling a small hole on the side of the sockolet to easier purge?
I guess there is a common used way to do it.
Thanks
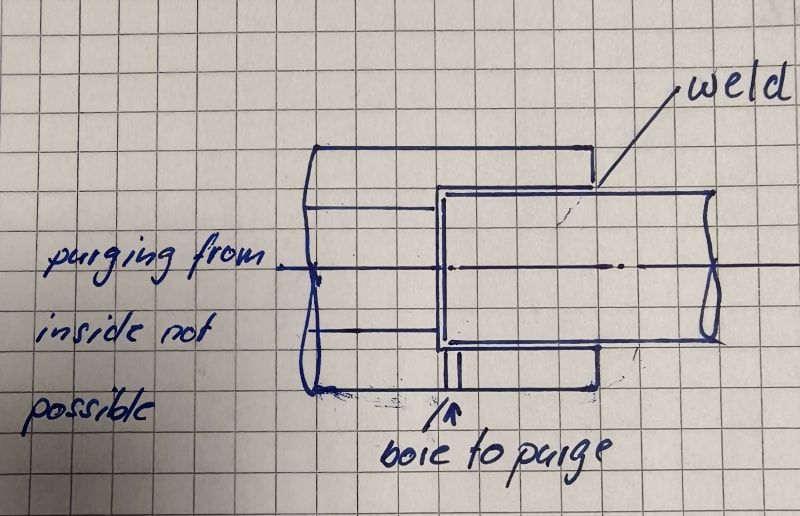