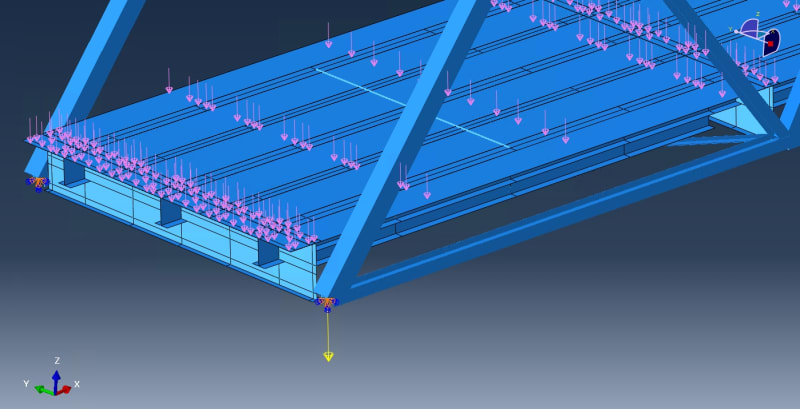
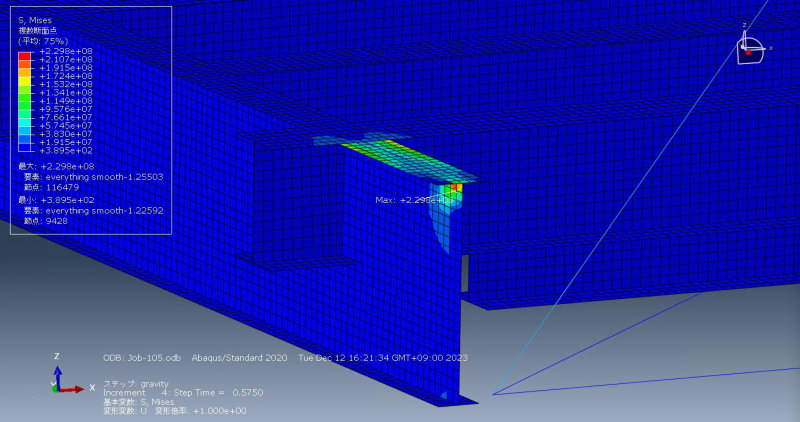
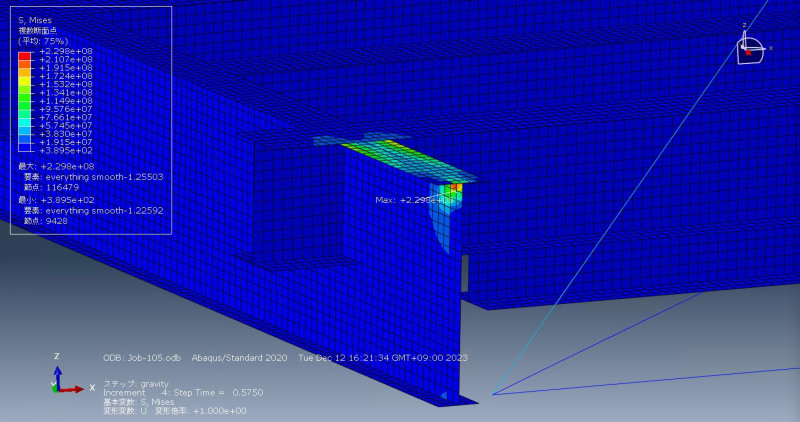
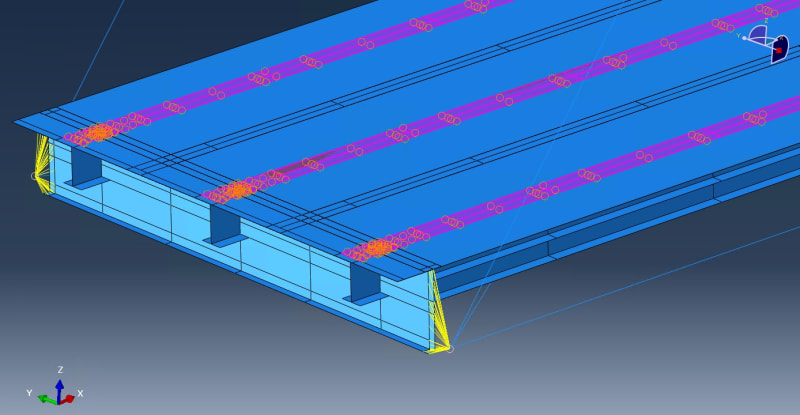
I am doing the simulation of a truss bridge with concrete deck in abaqus.
There is a problem that there is typical stress concentration around the top flange of crossbeam and I don't know how to solve it.
The truss is built with beam element and other parts in shell.
The boundary condition I use is all fixed at the southern 2 nodes and u1 and ur2 allowed at the other 2 support nodes.And I set tie interaction between concrete deck and longitudinal beam, and coupling between edge of crossbeam and truss node.
Now I just apply gravity of the whole structure and pressure as the mass of asphalt. But the stress concentration always exists.
Could anyone of you give me some advice?