wangrich
Mining
- Jun 27, 2024
- 2
This project is mainly used for domestic water supply, hydrant water supply, spray water supply, fountains, afforestation sprinkler irrigation, and other water supplies in the office building, exhibition center, and comprehensive business building in the project. This project adopts steel mesh skeleton-reinforced composite plastic pipe hot melt welding. The total length of the pipeline is about 3000 meters, and the pipe diameter is DN200.
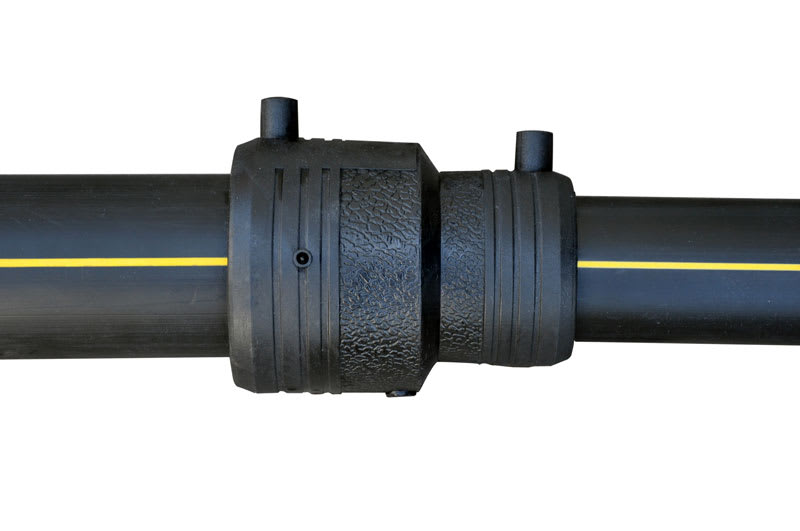
The working principle of wire mesh skeleton reinforced composite plastic pipe electric fusion welding:
Electric fusion welding is the latest popular welding method for steel wire mesh skeleton-reinforced composite plastic pipes. The principle is that the pipe socket is inserted in the pipe fitting, the resistance wire embedded in the inner surface of the fuse pipe fitting is energized and heated, the heat energy generated is heated, the inner surface of the fuse pipe fitting and the outer surface of the pipe socket with it are melted, and the cooling makes them integrated.
Construction process:
Welding equipment preparation → on-site inspection and pretreatment of pipes and fittings → Handling and installation of pipes and fittings → Adjustment of fixed joints of pipe retractable support → Electric fusion welding → Cooling → Disassembling pipe retractable support → Backfill to -500mm→ Sectional pressure test → overall backfill
Innovation of wire mesh skeleton reinforced composite plastic pipe fusion welding:
(1) The retractable pipe support developed on site is used in electric fusion welding in pipelines, which can ensure the reliable connection of welded joints, good sealing, and flatness of pipelines.
(2) The pipeline adopts electric fusion welding without welding materials such as welding wire, and the node strength is high, which completely solves the problems of leakage at the interface, reducing the leakage rate of the pipeline system and secondary pollution of the water supply network to the water quality.
(3) When the pipeline is backfilled with soil, the concrete thrust protection pier is set at the corner so that the pipeline is backfilled when the water is discharged, and there is no pipeline displacement and damage to the pipeline
(4) The pipeline is laid on rammed fill or old soil, and laid along the ground slope under the premise of meeting the buried depth, avoiding the traditional process of using C20 concrete cushion to control the bottom elevation of the pipe and other shortcomings, which greatly saves the construction cost and speeds up the construction progress.
(5) The pipeline test pressure was carried out according to domestic water supply 1.6Mpa, fire hydrant water supply 1.7Mpa, and spray water supply 1.8Mpa, and the test results showed no pressure drop and no leakage. It greatly exceeds the traditional process pressure test value of 0.6Mpa.
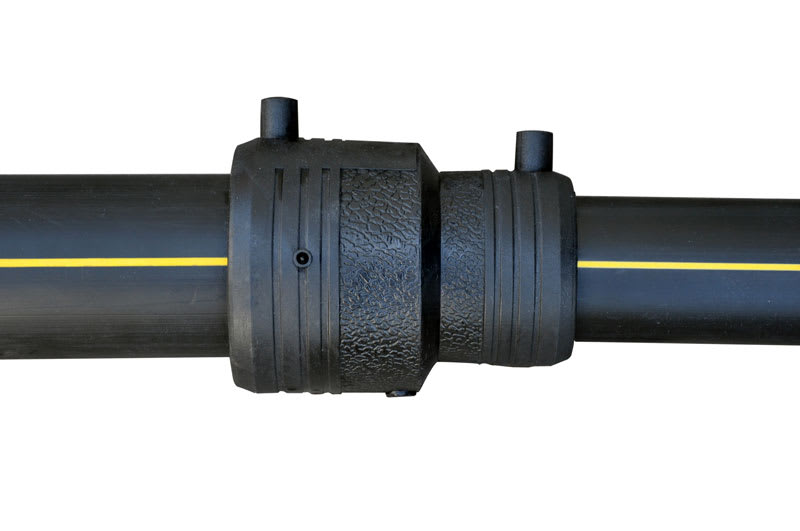
The working principle of wire mesh skeleton reinforced composite plastic pipe electric fusion welding:
Electric fusion welding is the latest popular welding method for steel wire mesh skeleton-reinforced composite plastic pipes. The principle is that the pipe socket is inserted in the pipe fitting, the resistance wire embedded in the inner surface of the fuse pipe fitting is energized and heated, the heat energy generated is heated, the inner surface of the fuse pipe fitting and the outer surface of the pipe socket with it are melted, and the cooling makes them integrated.
Construction process:
Welding equipment preparation → on-site inspection and pretreatment of pipes and fittings → Handling and installation of pipes and fittings → Adjustment of fixed joints of pipe retractable support → Electric fusion welding → Cooling → Disassembling pipe retractable support → Backfill to -500mm→ Sectional pressure test → overall backfill
Innovation of wire mesh skeleton reinforced composite plastic pipe fusion welding:
(1) The retractable pipe support developed on site is used in electric fusion welding in pipelines, which can ensure the reliable connection of welded joints, good sealing, and flatness of pipelines.
(2) The pipeline adopts electric fusion welding without welding materials such as welding wire, and the node strength is high, which completely solves the problems of leakage at the interface, reducing the leakage rate of the pipeline system and secondary pollution of the water supply network to the water quality.
(3) When the pipeline is backfilled with soil, the concrete thrust protection pier is set at the corner so that the pipeline is backfilled when the water is discharged, and there is no pipeline displacement and damage to the pipeline
(4) The pipeline is laid on rammed fill or old soil, and laid along the ground slope under the premise of meeting the buried depth, avoiding the traditional process of using C20 concrete cushion to control the bottom elevation of the pipe and other shortcomings, which greatly saves the construction cost and speeds up the construction progress.
(5) The pipeline test pressure was carried out according to domestic water supply 1.6Mpa, fire hydrant water supply 1.7Mpa, and spray water supply 1.8Mpa, and the test results showed no pressure drop and no leakage. It greatly exceeds the traditional process pressure test value of 0.6Mpa.