TRAK.Structural
Structural
- Dec 27, 2023
- 315
I have a project where a client wants to remove a portion of an exterior load bearing wall in order to make a large opening to a rear addition. The wall supports the 2nd level floor, roof trusses, and brick veneer. I've seen some threads about brick veneer support with wood as it relates to the code but it's still a little gray to me. See below some options for the detailing. Option #1 is similar to what I see at garage openings in my area, but I don't love the torsion this puts on the girder. Option #2 eliminates (or drastically reduces) torsion but I'm not completely sure if it is technically permitted. Option #3 is similar to #2 but just with a steel beam. The span is 19 feet so #3 may win out just due to load and deflection criteria but I'd like to know how others would approach the detailing to this.
Lastly, does this kind of change warrant cutting in vertical joints to the brick at both sides of the new girder?
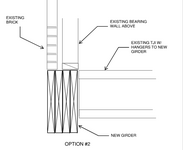
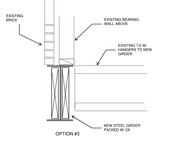
Lastly, does this kind of change warrant cutting in vertical joints to the brick at both sides of the new girder?
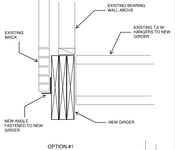
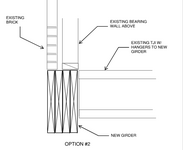
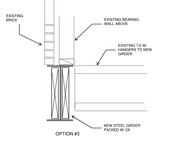