FlashPurp
Industrial
- May 10, 2024
- 13
Hello,
We are planning on using A333 Gr 6 piping in our design. The MDMT in B31.3 is -50 F and we have design conditions that may reach -55 F. I was told by by using the load case referenced
in B31.3 323.2.2 (a)(3) below and by reaching a stress ratio no greater the 0.95 that A333 Gr 6 material will be suitable to use at -55 F.
Referencing (23a) thru (23d) the equations given are only sustained loads. Do I only need to check the calculated sustained stress ratio to allowable stress but use 1 for the in-plane/out-plane moments? Would I use the allowable stress at MDMT? I am using Caesar II for stress calcs.
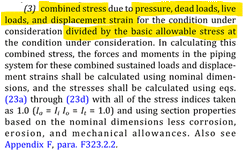
Thanks,
We are planning on using A333 Gr 6 piping in our design. The MDMT in B31.3 is -50 F and we have design conditions that may reach -55 F. I was told by by using the load case referenced
in B31.3 323.2.2 (a)(3) below and by reaching a stress ratio no greater the 0.95 that A333 Gr 6 material will be suitable to use at -55 F.
Referencing (23a) thru (23d) the equations given are only sustained loads. Do I only need to check the calculated sustained stress ratio to allowable stress but use 1 for the in-plane/out-plane moments? Would I use the allowable stress at MDMT? I am using Caesar II for stress calcs.
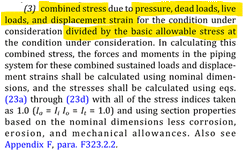
Thanks,