Sam165
Structural
- Sep 28, 2020
- 12
I recently finished a structural assessment on a church building that was built in 1917. The building is comprised of 55-foot long 9-ply wood trusses with 2x8 roof joists spanning 12-feet at 16-inches on-center perpendicular to the trusses. There are two specific deficiencies that I would like to pick your brain on:
1) There are a couple of 2x8 joists at each bay that are notched at the end bearing and this has caused the member to split parallel to the wood grain (see attached pictures). I ran a calculation (see attached) to determine the shear strength of the notched member and determined that I would need two LSL members sistered on both sides of the joist to reinforce it. What is the best way to reinforce this type of notch?
2) The truss members are attached with 1-inch thick plates (iron?) and 0.75-inch diameter through bolts. Many of the square nuts are missing and some of the bolts are too short or long to get a nut to tighten against the plate. There is one particular plate that has a hairline fracture that runs through the entire plate section. I'm thinking of reinforcing this plate with a steel plate that is placed in front of it and specifying replacement bolts for all areas that require them. I'm hoping they can get these old rusted bolts out to replace them. In addition, I was wondering if I can have them add a wood shim to the bolts that are too long so they can get the nut to tighten against that. What issues might that create?
Thanks for your help.
Sam
1) There are a couple of 2x8 joists at each bay that are notched at the end bearing and this has caused the member to split parallel to the wood grain (see attached pictures). I ran a calculation (see attached) to determine the shear strength of the notched member and determined that I would need two LSL members sistered on both sides of the joist to reinforce it. What is the best way to reinforce this type of notch?
2) The truss members are attached with 1-inch thick plates (iron?) and 0.75-inch diameter through bolts. Many of the square nuts are missing and some of the bolts are too short or long to get a nut to tighten against the plate. There is one particular plate that has a hairline fracture that runs through the entire plate section. I'm thinking of reinforcing this plate with a steel plate that is placed in front of it and specifying replacement bolts for all areas that require them. I'm hoping they can get these old rusted bolts out to replace them. In addition, I was wondering if I can have them add a wood shim to the bolts that are too long so they can get the nut to tighten against that. What issues might that create?
Thanks for your help.
Sam
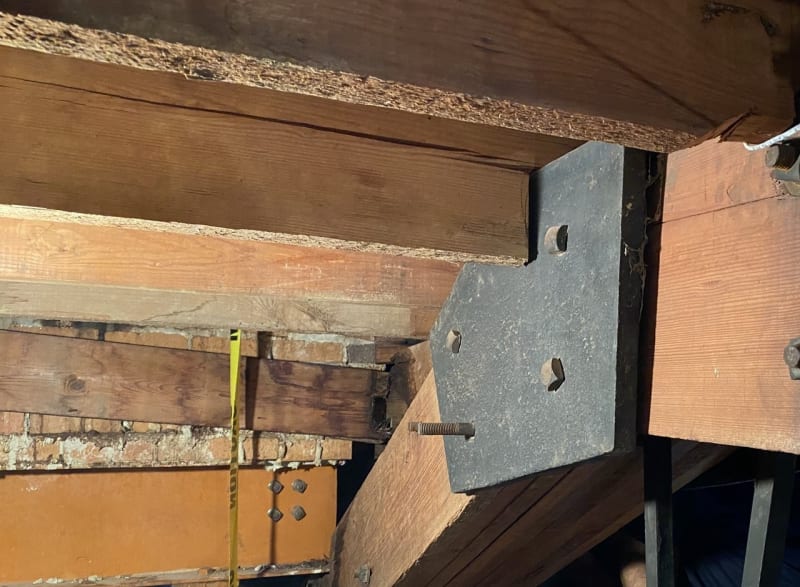
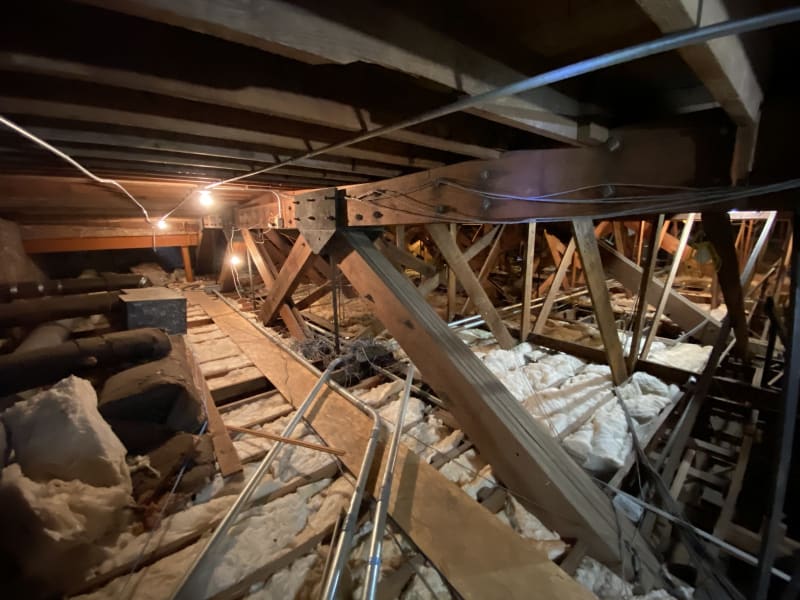

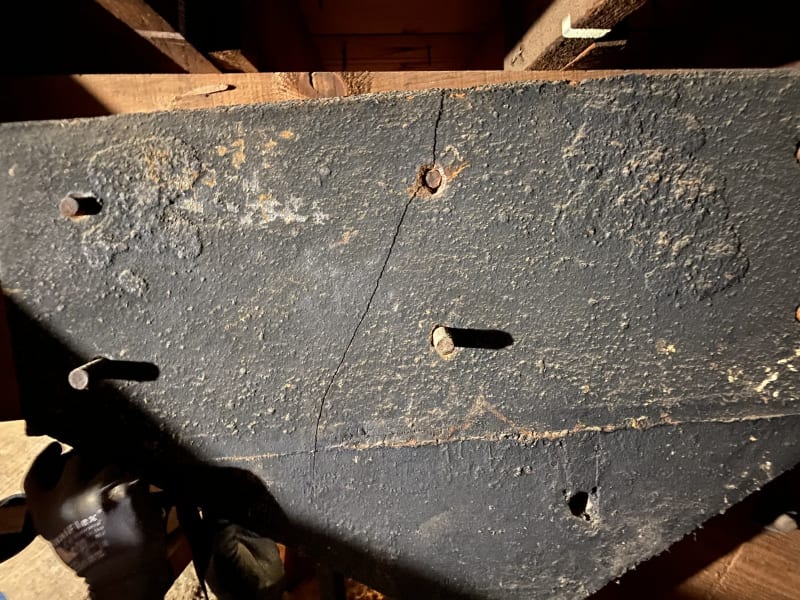
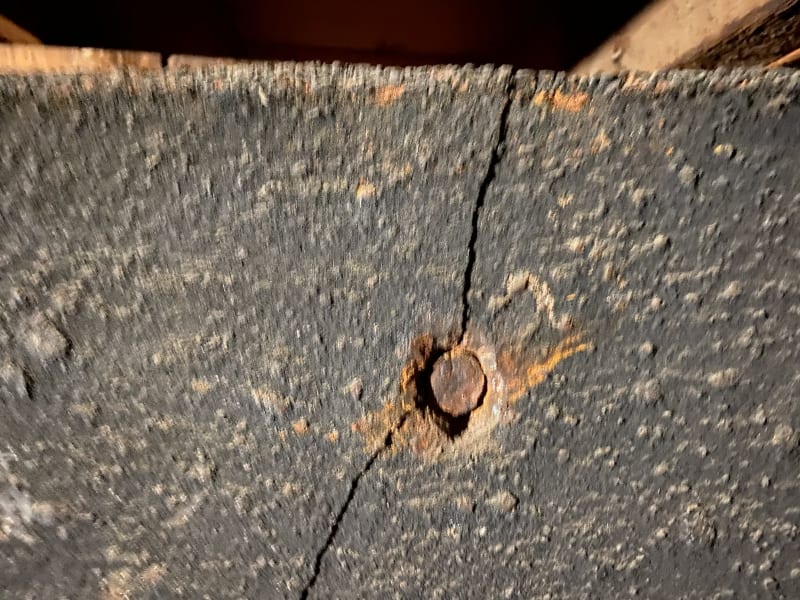
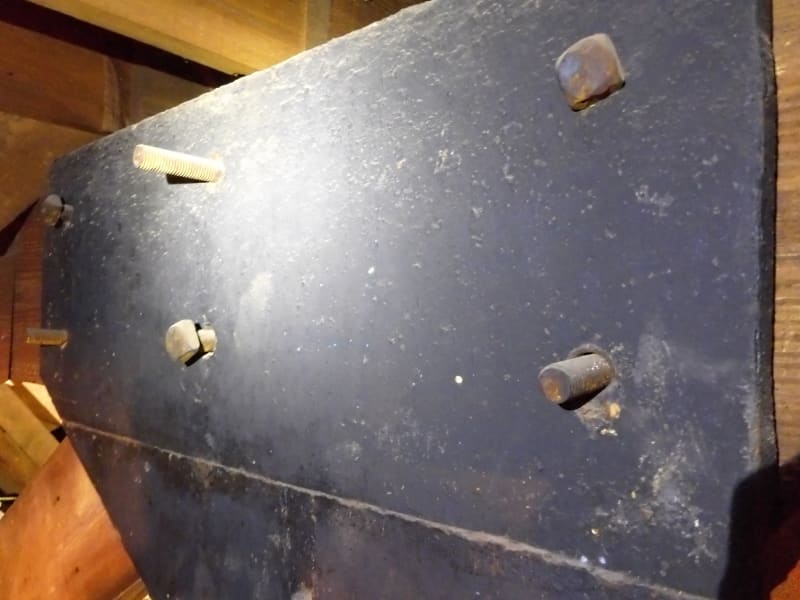