Texas Bricklady
Materials
- Apr 2, 2024
- 2
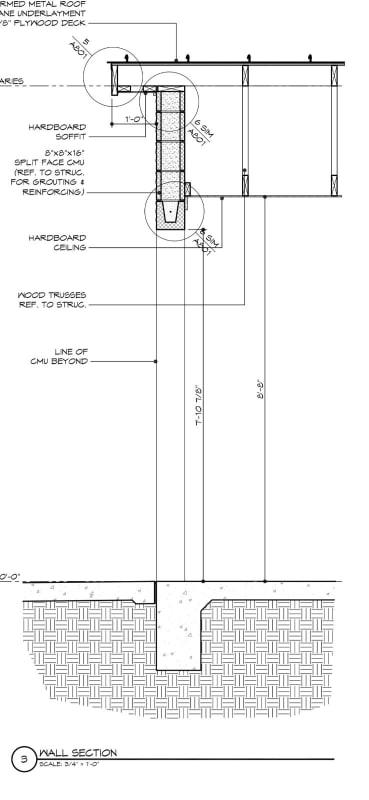
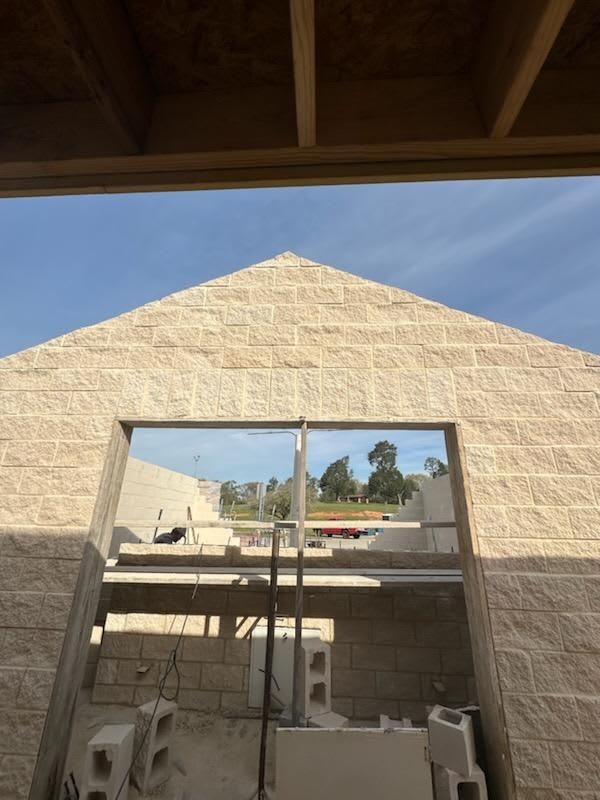

The bond beams span an 8'8" opening in a CMU wall.The drawings show 8" knockout bond beams. As a company that have done many buildings we felt we needed to use 16" horse collar (deep)bond beams. Also he had only one rebar that flowed all the way through and we added the second one to go all the way through too. We got permission to change the bond beam type both GC and owner agreed but now the architect (and his engineer) are saying we in fact weakend the structure. We of course strengthened it with the extra reinforcement.
Now we have to tear it out, get a structural engineer to agree that it's OK, or give them a lifetime guarantee instead of the standard 1 year warranty. Most architects understand the reasoning but he says he has never seen a 16" horsecollar and its not standard.
We are in Texas
Thanks