kruq
Structural
- Nov 22, 2017
- 9
Hi all,
I have question about connection like showed in attachment. I used to work with EC codes so for AISC I need support
I have two HSS cantilevers attached to HSS 6x6x5/8 column and two HSS beams which are extension for cantilevers to create kind of overhanged beams. On cantilevers there is bending momement 410 kip-in and shear force ~8.5 kip. My first question is can I use in this case 1+0.5sinθ factor for designing welds to column? Because by Chapter K in AISC it is prohibited but I would like to know Your opinion. Second question is do You think differences in outriggers depths will be problematic to transfer bending moments from cantilever to second side? I've checked plastification of HSS wall via chapter K3.2 but I am wondering what can happend on side walls if there are also welded outriggers to post. Thanks for answer.
I have question about connection like showed in attachment. I used to work with EC codes so for AISC I need support
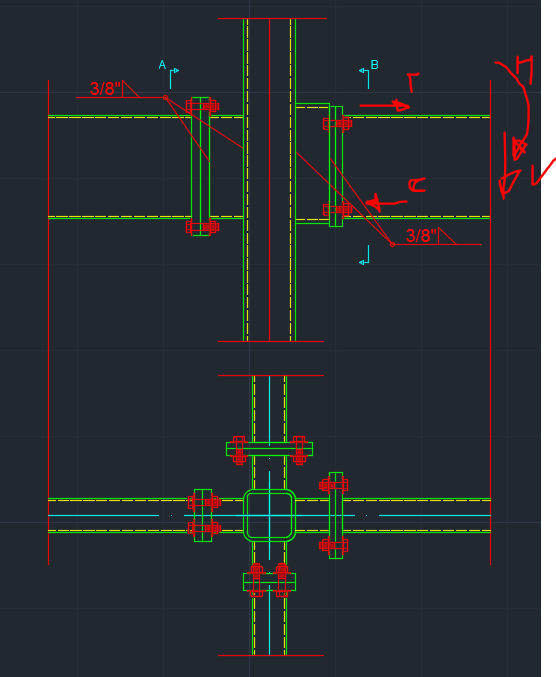