mechdrive1
Mechanical
Hello everyone ! this is my first thread and hope that I get valuable suggestions from the experienced persons in this forum ! below is the description of my problem-
"I'm modeling a friction based welding process which involves a rigid tool being inserted into a deformable (Aluminium alloy) workpiece. I've used Johnson-cook plastic hardening with Johnson-cook rate dependency (initially it was the plasticity) to see if has some +ve effects on my model, but it didnt. I have used C3D8RT elements for both tool and workpiece.I've used a fine mesh for the interaction region (for tool and workpiece) and coarse mesh otherwise. The tool has an angular velocity of 400 rads/sec with a feed rate of 0.5 mm/sec whereas the bottom surfaces of workpiece are encastre'd. I've given the movement to the tool by using 'tabular' amplitude increasing in paced manner. In the step, i've specified non-linear geometry with mass scaling for the concerned interaction (tool & workpiece) region (factor-10^8) at the beginning of step (it does increase the stable time increment). I've used ALE adaptive meshing with a frequency of 1 and remshing sweeps as 50-75, I've chosen frequency of 1 so that I can specify ALE mesh constraint for the workpiece (only the region where tool is inserted). I even tried element deletion, although I didnt specify any damage criteria in material module (dont know if it's necessary). the total time period of my analysis is 4 seconds and a pressure of 80Mpa is applied on the tool. I would like to clarify that I've checked the units of the material properties 'n' number of times and there's no worry over there. Whenever i run the analysis, the model reaches a time period of only 0.86 seconds with stable time increment of 1.0E-6. the mesh gets excessively distorted and analysis is aborted.
I am attaching images of the meshed assembly and also models.
---->
---->
----->
----->
Please anyone who has knowledge about this issue or have faced same problem, give your suggestion/advise that can be used to resolve this issue. I've tried looking in literature of similar processes for a solution, but couldnt find any !
Thanks in advance !!
"I'm modeling a friction based welding process which involves a rigid tool being inserted into a deformable (Aluminium alloy) workpiece. I've used Johnson-cook plastic hardening with Johnson-cook rate dependency (initially it was the plasticity) to see if has some +ve effects on my model, but it didnt. I have used C3D8RT elements for both tool and workpiece.I've used a fine mesh for the interaction region (for tool and workpiece) and coarse mesh otherwise. The tool has an angular velocity of 400 rads/sec with a feed rate of 0.5 mm/sec whereas the bottom surfaces of workpiece are encastre'd. I've given the movement to the tool by using 'tabular' amplitude increasing in paced manner. In the step, i've specified non-linear geometry with mass scaling for the concerned interaction (tool & workpiece) region (factor-10^8) at the beginning of step (it does increase the stable time increment). I've used ALE adaptive meshing with a frequency of 1 and remshing sweeps as 50-75, I've chosen frequency of 1 so that I can specify ALE mesh constraint for the workpiece (only the region where tool is inserted). I even tried element deletion, although I didnt specify any damage criteria in material module (dont know if it's necessary). the total time period of my analysis is 4 seconds and a pressure of 80Mpa is applied on the tool. I would like to clarify that I've checked the units of the material properties 'n' number of times and there's no worry over there. Whenever i run the analysis, the model reaches a time period of only 0.86 seconds with stable time increment of 1.0E-6. the mesh gets excessively distorted and analysis is aborted.
I am attaching images of the meshed assembly and also models.
---->
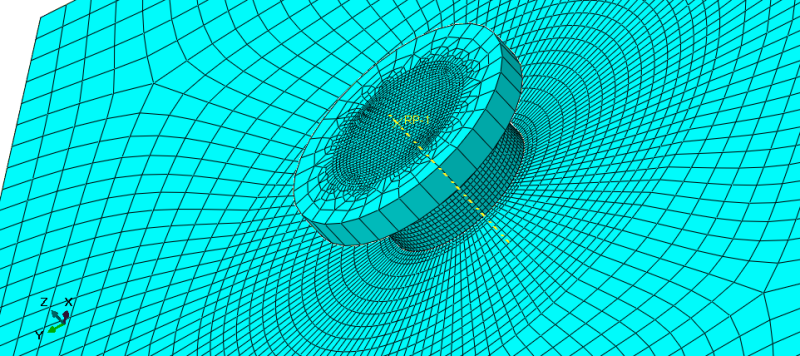
---->
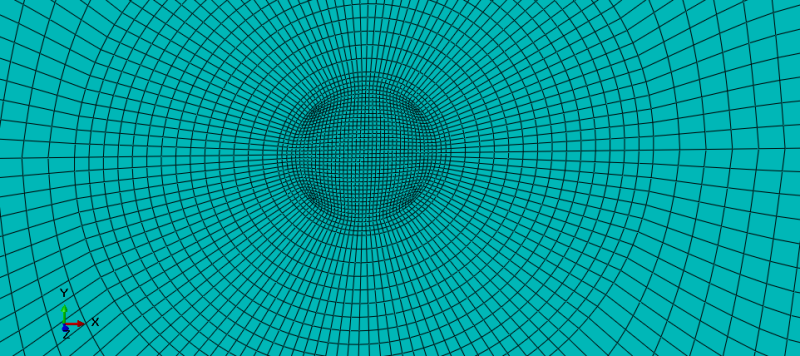
----->
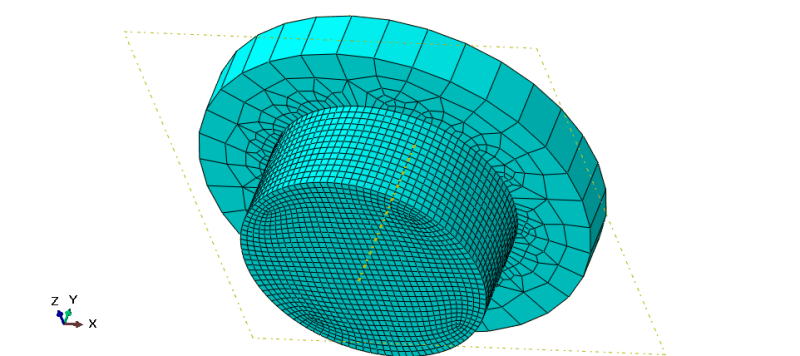
----->
Please anyone who has knowledge about this issue or have faced same problem, give your suggestion/advise that can be used to resolve this issue. I've tried looking in literature of similar processes for a solution, but couldnt find any !
Thanks in advance !!