I am currently modelling a plate with 3D elements (just 1 element thru thickness):
I have applied a displacement BC on the right surface, as well as restraining moments. I have fixed the left face as shown in the image above.
I am looking to determine a stress vs strain plot, as per this thread. similar to what you get from testing
However, I'm not sure how I would go about this problem on my side, due to the moment constraints on the RHS surface.
Therefore, I have currently output the nodal force at a location on the RH face with time and multiplied it with the total number of nodes on the RH face (to get the total nodal force as a close approximation). I then divide this total nodal force by the area to get the stress on the RH face. I have then output displacement at that node with a function of time, and can convert this to strain via post processing.
What do you think of this method? The reaction force and Ux displacement is constant on the RH surface due to the applied BC.
Any suggestions welcome.
Thanks
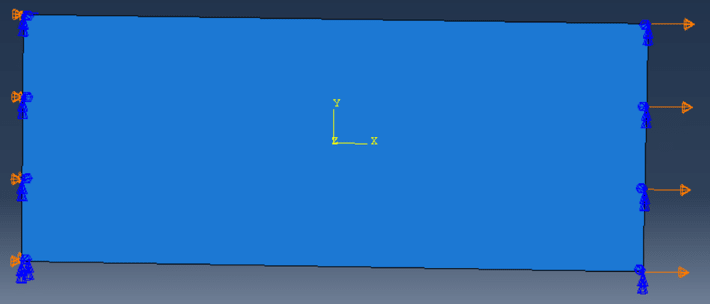
I have applied a displacement BC on the right surface, as well as restraining moments. I have fixed the left face as shown in the image above.
I am looking to determine a stress vs strain plot, as per this thread. similar to what you get from testing
However, I'm not sure how I would go about this problem on my side, due to the moment constraints on the RHS surface.
Therefore, I have currently output the nodal force at a location on the RH face with time and multiplied it with the total number of nodes on the RH face (to get the total nodal force as a close approximation). I then divide this total nodal force by the area to get the stress on the RH face. I have then output displacement at that node with a function of time, and can convert this to strain via post processing.
What do you think of this method? The reaction force and Ux displacement is constant on the RH surface due to the applied BC.
Any suggestions welcome.
Thanks