-
1
- #1
andreadelvecchio
Structural
hello to everybody, I am attaching pictures of my problem.
the first picture is the undeformed of my first approach, a ribbon wound around a reel.
in the second picture I've try to applied several load to close the ribbon.
there is friction between the reel and ribbon. it work fine.
then I wanted to add another ribbon (figure 3 and 4) and do the same, but it doesn'd work.
the analysis does not increase. I dont'n know if it is a problem of mesh or contact or both of them.
any advice is welcome. thanks to all
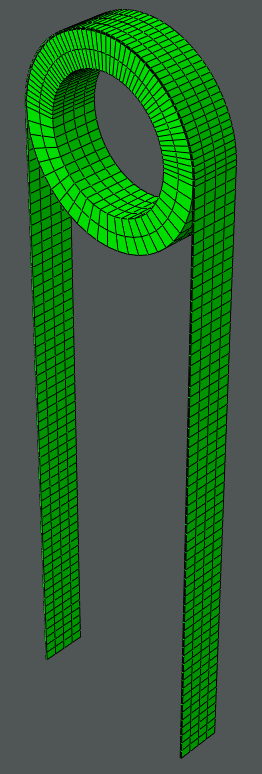
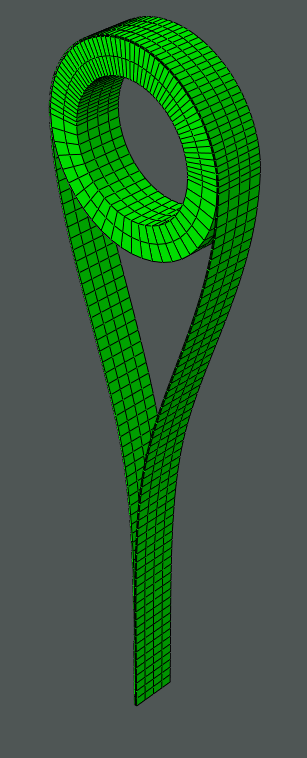
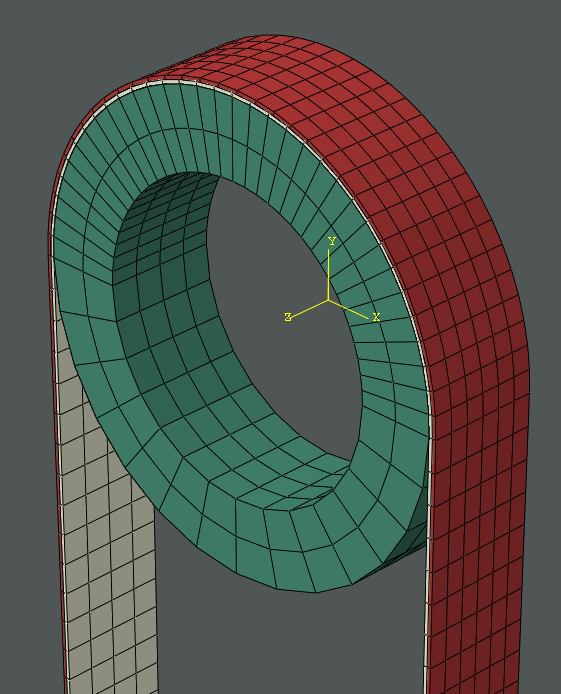
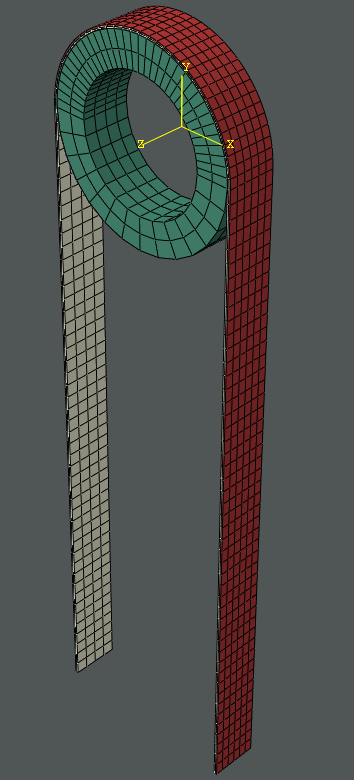
the first picture is the undeformed of my first approach, a ribbon wound around a reel.
in the second picture I've try to applied several load to close the ribbon.
there is friction between the reel and ribbon. it work fine.
then I wanted to add another ribbon (figure 3 and 4) and do the same, but it doesn'd work.
the analysis does not increase. I dont'n know if it is a problem of mesh or contact or both of them.
any advice is welcome. thanks to all