Hello there, I went to a learning visit to a plant where there's a problem with air getting trapped into a pump moving cooling tower water towards an heat exchanger. They can't quite figurer out why air could get there since the pump is positioned 2,5 m (8 ft.) under the cooling tower basin, so the NPSH available should always be greater than the one required. The cooling tower is used in a batch production, so it's often shut down to be turned on again later.
Could it be because of a pan-drain down during the start up phase ? I noticed how the basin volume looks very small compared to the pipeline circuit and heat exchanger that would have to be filled before sending back the water to the top of the cooling tower. I also noticed there's no check valve installed so I suppose the pipeline circuit doesn't stay flooded after each shut down of the cooling tower. (could this be determined by looking if Volume_pipeline + V_heat exchanger > V_tower basin ?)
Or should they not overlook the possibility of having air getting stuck in the vertical drop after the cooling tower basin ?
Could a solution be to place an additional tank to provide the additional volume needed to fill the whole circuit ? Or should they place valves to prevent piping to tower drainage (pic below)
Sorry if something I said might sound silly, I'm just trying to learn and my professor didn't have an answer for me. Many thanks in advance ! (I attached a sketch of the circuit)
Could it be because of a pan-drain down during the start up phase ? I noticed how the basin volume looks very small compared to the pipeline circuit and heat exchanger that would have to be filled before sending back the water to the top of the cooling tower. I also noticed there's no check valve installed so I suppose the pipeline circuit doesn't stay flooded after each shut down of the cooling tower. (could this be determined by looking if Volume_pipeline + V_heat exchanger > V_tower basin ?)
Or should they not overlook the possibility of having air getting stuck in the vertical drop after the cooling tower basin ?
Could a solution be to place an additional tank to provide the additional volume needed to fill the whole circuit ? Or should they place valves to prevent piping to tower drainage (pic below)
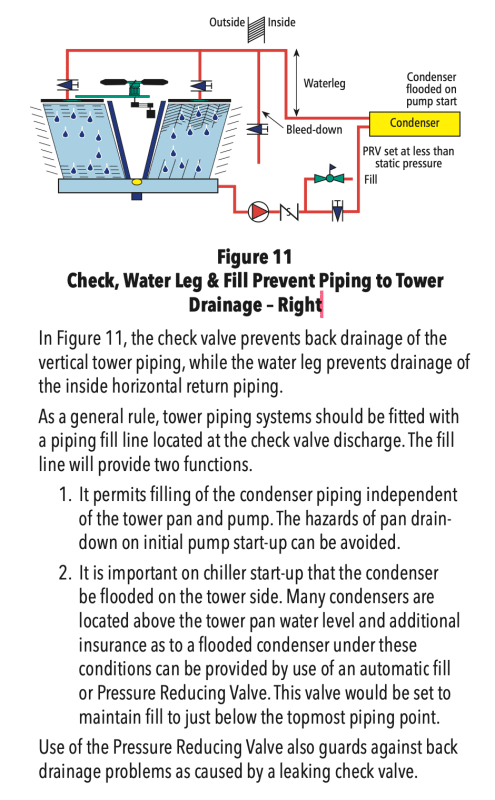
Sorry if something I said might sound silly, I'm just trying to learn and my professor didn't have an answer for me. Many thanks in advance ! (I attached a sketch of the circuit)