Agatha_012
Mechanical
- Mar 25, 2022
- 7
Hello, I am currently working on developing a soft tentacle arm robot, that can work in close proximity to humans. I initially intended it to be entirely made out of silicone. However, it seems it's not possible to make a silicone robot both soft and strong at the same time.
So, I came up with 2 designs, but can't choose.
1. The tentacle is divided into 8-10 sections horizontally; each section having 4 air muscles, that will be individually controlled through air vessels and a solenoid valve mechanism.
2. The tentacle is again divided into 8-10 sections horizontally. However, this time, it will be controlled with a compliant mechanism mostly inspired by a compliant gripper. Here, I am planning to incorporate a solenoid valve mechanism into each section. Using electricity, I am planning to control the direction of the bending.
Would appreciate any thoughts and discussions on this.
Note: This is not the final design yet. Both versions need a lot of improvement. The question is, which one is worth investing more time in?
So, I came up with 2 designs, but can't choose.
1. The tentacle is divided into 8-10 sections horizontally; each section having 4 air muscles, that will be individually controlled through air vessels and a solenoid valve mechanism.
2. The tentacle is again divided into 8-10 sections horizontally. However, this time, it will be controlled with a compliant mechanism mostly inspired by a compliant gripper. Here, I am planning to incorporate a solenoid valve mechanism into each section. Using electricity, I am planning to control the direction of the bending.
Would appreciate any thoughts and discussions on this.
Note: This is not the final design yet. Both versions need a lot of improvement. The question is, which one is worth investing more time in?
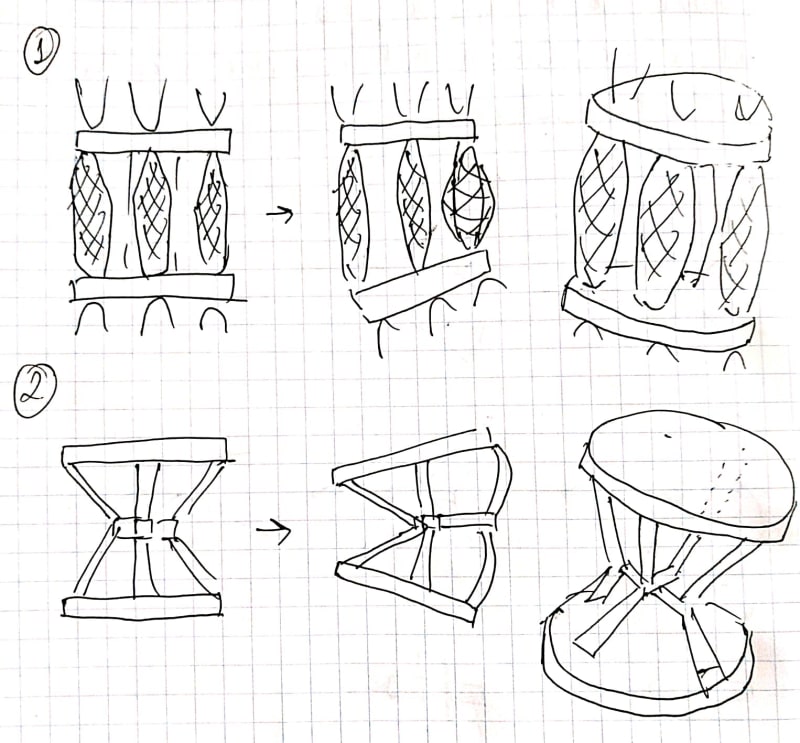