Here's another one that looks simple but is actually not.
I thought the best way to describe what I want to do was to sketch a wonky drawing of my requirement:
So Datum A is defined as the axis of the small diameter.
Datum B is then to be perpendicular to Datum A (if required).
Then I wish to define the 42 mm dimension, but the direction the dimension should be measured should be aligned with datum A and be the taken from the most distant points on the two surfaces.
I'm working in ISO so rule 1 isn't default but may be useful to apply?
Technically the 42 mm dimension only needs to apply between datum B and a circular boundary on the rightmost face, but let's walk before we run.
Any help would be greatly appreciated. Maybe it's all dead simple and I'm just too far down a rabbit hole to see the light of day. Here's to hoping hey.
I thought the best way to describe what I want to do was to sketch a wonky drawing of my requirement:
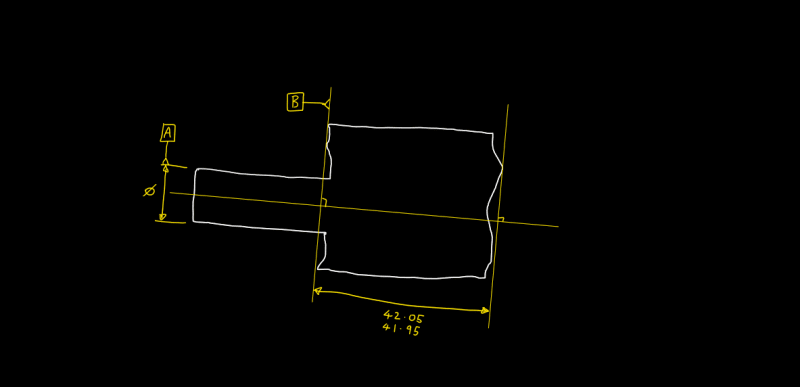
So Datum A is defined as the axis of the small diameter.
Datum B is then to be perpendicular to Datum A (if required).
Then I wish to define the 42 mm dimension, but the direction the dimension should be measured should be aligned with datum A and be the taken from the most distant points on the two surfaces.
I'm working in ISO so rule 1 isn't default but may be useful to apply?
Technically the 42 mm dimension only needs to apply between datum B and a circular boundary on the rightmost face, but let's walk before we run.
Any help would be greatly appreciated. Maybe it's all dead simple and I'm just too far down a rabbit hole to see the light of day. Here's to hoping hey.