SwaggingIt
Mechanical
I havent been a gear designer for a long time, but I'm following AGMA 2001 and my values are verified by KISSsoft. So because I havent been designing gears for long, I'm not sure how to deal with this situation:
Gear pair is 48 pitch with driver spinning at 1686 RPM worst case for only 4.44 hours at this max operating condition.
Material is 15-5 through hardened to 42 HRC (392 HB). I use table 9 in AGMA 2001 to determine Sat then apply the factors in the image to get my acceptable stress of 49.6 ksi. Shigley states that the endurance strength for steels is 0.5*Sy so this would be 72.5 ksi for 15-5. How do I reconcile what AGMA says versus what Shigley says? Is AGMA just too conservative when it comes to fine pitch high speed gears, so I should consider Shigley's endurance strength in these instances? But I would still use AGMA calculation for the bending stress number which is essentially applying the stress modifiers in the Shigley version.
Been spinning my wheels over this for a while now and just need the most logical way to defend my design to the customer. Thank you for any feedback!
P.S. the YM factor is because I'm expecting oscillation and this factor is "from" ISO 6336.
Gear pair is 48 pitch with driver spinning at 1686 RPM worst case for only 4.44 hours at this max operating condition.
Material is 15-5 through hardened to 42 HRC (392 HB). I use table 9 in AGMA 2001 to determine Sat then apply the factors in the image to get my acceptable stress of 49.6 ksi. Shigley states that the endurance strength for steels is 0.5*Sy so this would be 72.5 ksi for 15-5. How do I reconcile what AGMA says versus what Shigley says? Is AGMA just too conservative when it comes to fine pitch high speed gears, so I should consider Shigley's endurance strength in these instances? But I would still use AGMA calculation for the bending stress number which is essentially applying the stress modifiers in the Shigley version.
Been spinning my wheels over this for a while now and just need the most logical way to defend my design to the customer. Thank you for any feedback!
P.S. the YM factor is because I'm expecting oscillation and this factor is "from" ISO 6336.
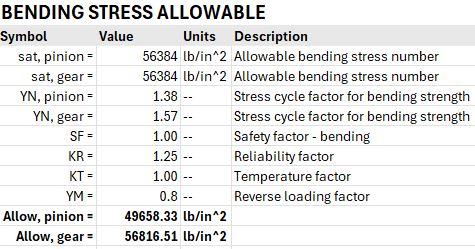