Eng_Struct
Structural
Hi Group,
I need to reinforce the bottom chord of an existing OWSJ and I am considering a steel plate welded to the bottom chord. The plate will extend past the toe of the existing angle toe on both sides so that a weld can be made from above. For fillet welds between the round toe of rolled section and the plate, the code allows you to consider only 3/4 of the thickness of the rolled section for weld size (see image below). My challenge is that the resulting fillet weld thickness based on this requirement does not get me the strength I need for the weld.
I guess I can always increase the length of the fillet weld to compensate for the reduction of weld thickness but want to know if there are any other types of welds that can be specified for this particular application.
Thanks!
I need to reinforce the bottom chord of an existing OWSJ and I am considering a steel plate welded to the bottom chord. The plate will extend past the toe of the existing angle toe on both sides so that a weld can be made from above. For fillet welds between the round toe of rolled section and the plate, the code allows you to consider only 3/4 of the thickness of the rolled section for weld size (see image below). My challenge is that the resulting fillet weld thickness based on this requirement does not get me the strength I need for the weld.
I guess I can always increase the length of the fillet weld to compensate for the reduction of weld thickness but want to know if there are any other types of welds that can be specified for this particular application.
Thanks!
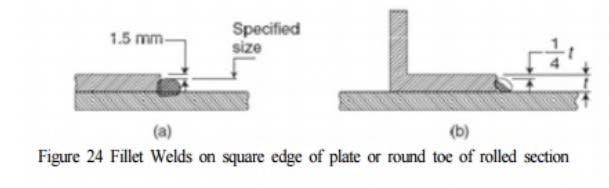