I am working with some legacy prints that make use of symmetry and concentricity. Looking for advice on alternative tolerance options that can replace these. I am fairly green to certain areas of GD&T and would appreciate some input.
Parts are mainly rotating steel shafts. Print below.
Correct me if I am wrong, but I believe the circular runout shown will control the concentricity to a degree. I am thinking of changing this to total runout (seems more appropriate here to control the whole surface) and removing the concentricity control altogether?
I get the idea of the symmetry to keep that 'socket' end centered on the A datum axis. What would be the best way to accomplish this?
Parts are mainly rotating steel shafts. Print below.
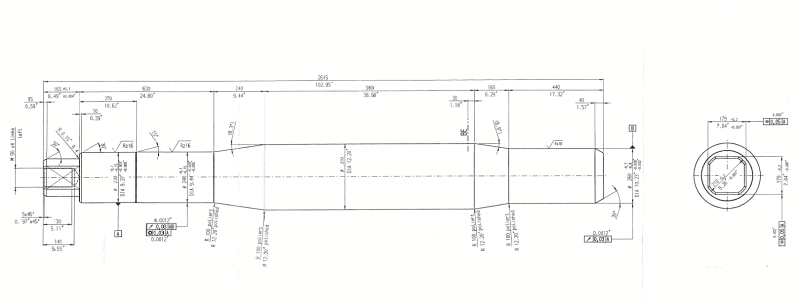
Correct me if I am wrong, but I believe the circular runout shown will control the concentricity to a degree. I am thinking of changing this to total runout (seems more appropriate here to control the whole surface) and removing the concentricity control altogether?
I get the idea of the symmetry to keep that 'socket' end centered on the A datum axis. What would be the best way to accomplish this?