Arbu
Structural
- Mar 25, 2018
- 69
Dear All,
I am designing a Steel Skylight in which beam supporting skylight has been connected with each other by a Hollow circular disc As shown in image below. All member are RHS/Tube 160x80x5 mm. each member is carrying major moment, Major shear and axial Compression/Tension. I am looking for some analysis method for the disc/Node connecting beams. Please suggest some method.
regards,
SigmaEng
I am designing a Steel Skylight in which beam supporting skylight has been connected with each other by a Hollow circular disc As shown in image below. All member are RHS/Tube 160x80x5 mm. each member is carrying major moment, Major shear and axial Compression/Tension. I am looking for some analysis method for the disc/Node connecting beams. Please suggest some method.
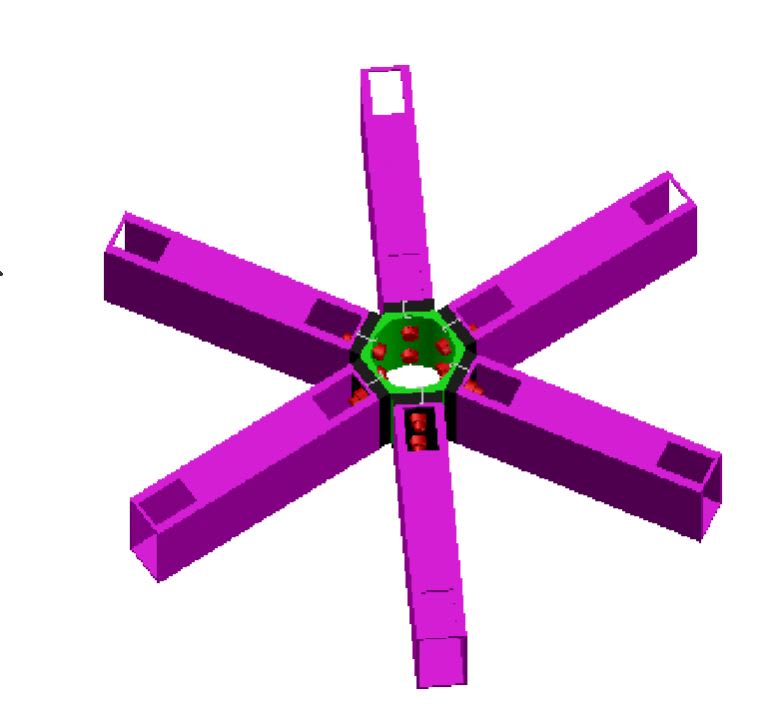
regards,
SigmaEng