I am working on the design of a concrete pipe support pedestal. The pedestal is supporting a 16" diameter pipe. The pipe is attached to a 90 degree elbow with a pressure of 130 psi. My pipe support is located above grade.
The resultant thrust force due to the 90 degree elbow is 37 kips ( Fx =Fy = 26.1 kips [force components]). This is based on the equation in the image below:
I have obtained a sample plan sheet of thrust blocks.
See this link for the example thrust blocks:
Based on the example drawing, it seems to me as if anchor bolts are not considered when design thrust block supports. Would this be an accurate statement? Since my 16" dia pipe is above grade, would my design be under a different criteria?
The initial concrete pedestal detail that I am revising has an anchor bolt shown.
There are initial a total of two anchor bolts (1 on each side of the pipe) that would be resisting a horizontal force of 26.1 kips coming thru the pipe.
I initial would think that the anchor bolts need to be able to resist the thrust forces applied by the elbow ( Fx =Fy = 26.1 kips [force components]). Is this accurate?
Suggestions/comments are appreciated.
The resultant thrust force due to the 90 degree elbow is 37 kips ( Fx =Fy = 26.1 kips [force components]). This is based on the equation in the image below:
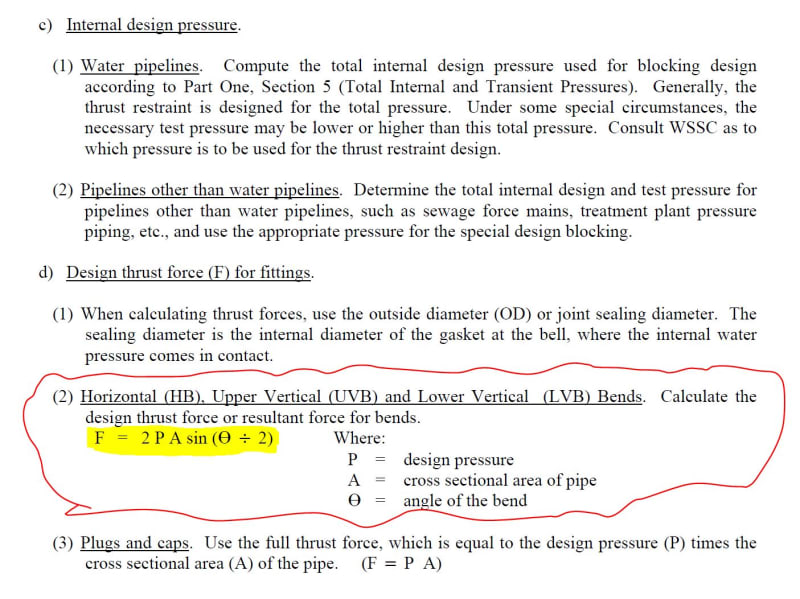
I have obtained a sample plan sheet of thrust blocks.
See this link for the example thrust blocks:
Based on the example drawing, it seems to me as if anchor bolts are not considered when design thrust block supports. Would this be an accurate statement? Since my 16" dia pipe is above grade, would my design be under a different criteria?
The initial concrete pedestal detail that I am revising has an anchor bolt shown.
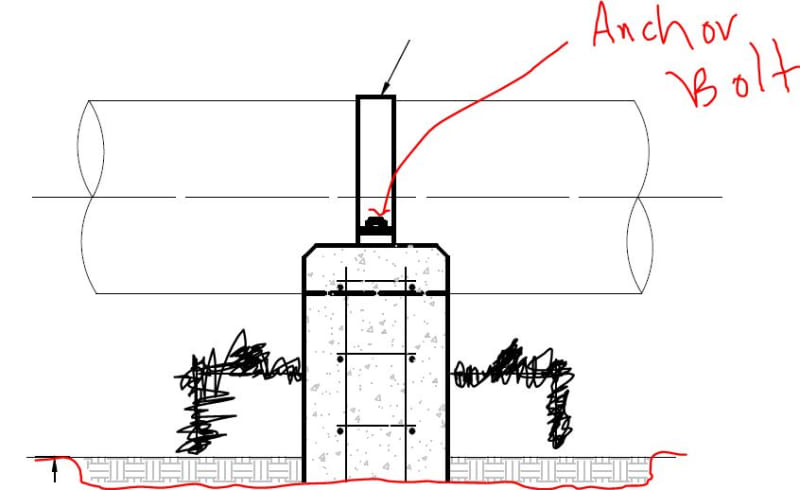
There are initial a total of two anchor bolts (1 on each side of the pipe) that would be resisting a horizontal force of 26.1 kips coming thru the pipe.
I initial would think that the anchor bolts need to be able to resist the thrust forces applied by the elbow ( Fx =Fy = 26.1 kips [force components]). Is this accurate?
Suggestions/comments are appreciated.