Looking for some input on design/evaluation of the situation below. Existing structure that my company owns which was engineered and recently built by others. I'm evaluating some changes to the loading. Foundation for a telecom tower with large (2400 ft-kips factored) overturning moments and fairly low (30 kips) axial loads. Anchor bolts are 18J bars that are threaded each end. While deformed, they're nowhere near enough embed to be developed in tension.
The pedestal was designed flexurally and the anchor bolt embed was evaluated to develop the pedestal reinforcing above the concrete breakout failure plane. This is how I typically see it for drilled pier foundations and it appears they applied the same logic here.
My issue is that the reinforcing is not developed below the anchor bolt concrete breakout failure plane. So I got into checking the concrete breakout strength in tension and my approach is leading to failure.
I analyzed the bolts about the Y axis in the pattern sketch below. So there are 4 bolts in tension, 2 on the neutral axis and 4 in compression (no grout). The axial loads skew towards compression by a few kips. Total tension in those 4 bolts was approximately 700 kips. With an heff of ~26" (using the 3' deep footing only), Anc for my odd 4 bolt pattern (shape is below) was 9573 and I get an phi-Ncbg of around 247 kips (way off).
So I guess my questions are these:
1. Should I have completely neglected the pedestal vertical reinforcing in my tension capacity? Can it assist at all?
2. My failure plane passes thru the pedestal which was cast integrally with the foundation. On that side it would pass thru reinforcing that is developed below. Any reasonable manner to consider that reinforcing?
3. Is it appropriate that I've completely neglected the anchor bolt deformations?
4. I did not consider the template embedded in the concrete to add to the Anc as it was only 1/4" thick. Too conservative? That would also increase my heff by a couple inches.
5. Any flaws in my general approach to this evaluation?
Input or questions welcome.
The pedestal was designed flexurally and the anchor bolt embed was evaluated to develop the pedestal reinforcing above the concrete breakout failure plane. This is how I typically see it for drilled pier foundations and it appears they applied the same logic here.
My issue is that the reinforcing is not developed below the anchor bolt concrete breakout failure plane. So I got into checking the concrete breakout strength in tension and my approach is leading to failure.
I analyzed the bolts about the Y axis in the pattern sketch below. So there are 4 bolts in tension, 2 on the neutral axis and 4 in compression (no grout). The axial loads skew towards compression by a few kips. Total tension in those 4 bolts was approximately 700 kips. With an heff of ~26" (using the 3' deep footing only), Anc for my odd 4 bolt pattern (shape is below) was 9573 and I get an phi-Ncbg of around 247 kips (way off).
So I guess my questions are these:
1. Should I have completely neglected the pedestal vertical reinforcing in my tension capacity? Can it assist at all?
2. My failure plane passes thru the pedestal which was cast integrally with the foundation. On that side it would pass thru reinforcing that is developed below. Any reasonable manner to consider that reinforcing?
3. Is it appropriate that I've completely neglected the anchor bolt deformations?
4. I did not consider the template embedded in the concrete to add to the Anc as it was only 1/4" thick. Too conservative? That would also increase my heff by a couple inches.
5. Any flaws in my general approach to this evaluation?
Input or questions welcome.
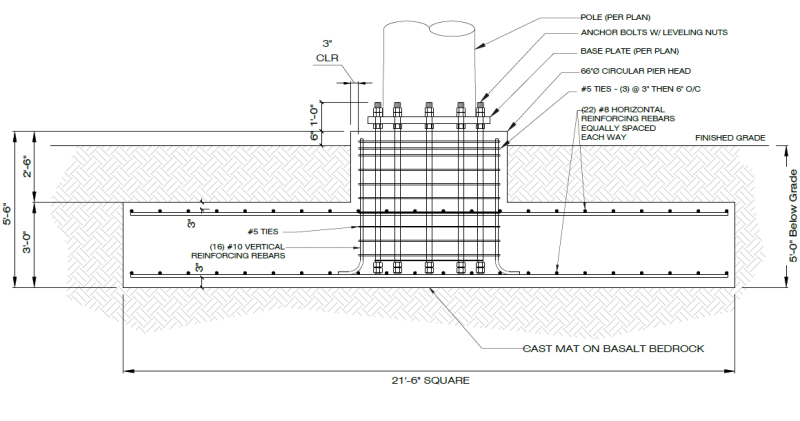
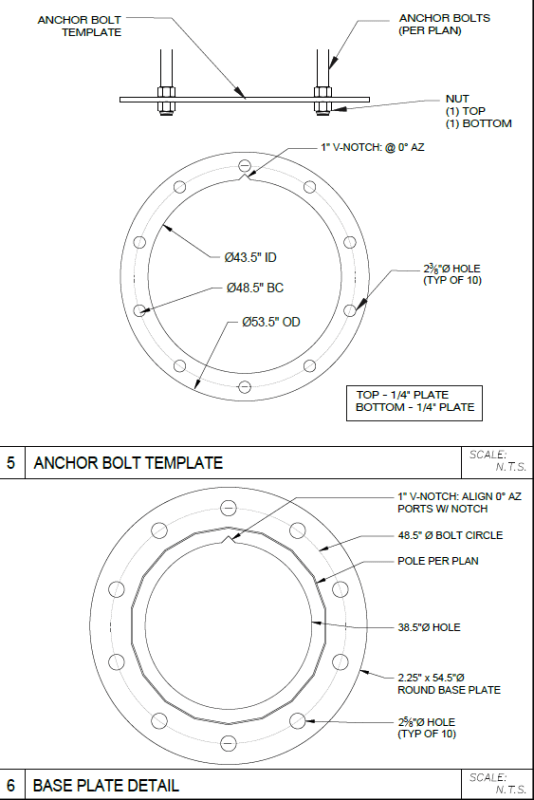
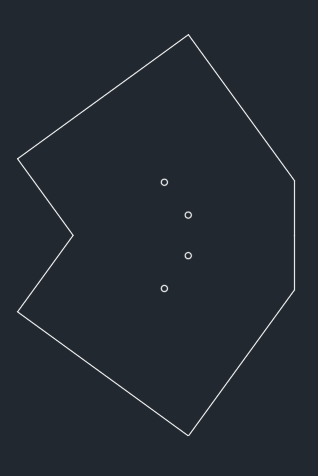