dreber
Civil/Environmental
- Feb 9, 2011
- 105
Hi folks, I couldn't find any guidance in the AISC 360, nor on my attempts at google searching, so I've invented a method and I thought I would run it by you folks for your input:
The Situation
I have a post welded to a base plate, the base plate is anchored to the concrete below via anchor bolts and leveling nuts. No non shrink grout here, just the anchor bolts to resist all forces.
This is putting my anchor bolts into shear, bending, and tension, and I don't know of any specific provisions for checking the combination of stresses on anchor bolts. So, I just added up all of ASD level DCRs and summed them. Does this sound like an appropriate approach to you?
The Situation
I have a post welded to a base plate, the base plate is anchored to the concrete below via anchor bolts and leveling nuts. No non shrink grout here, just the anchor bolts to resist all forces.
This is putting my anchor bolts into shear, bending, and tension, and I don't know of any specific provisions for checking the combination of stresses on anchor bolts. So, I just added up all of ASD level DCRs and summed them. Does this sound like an appropriate approach to you?
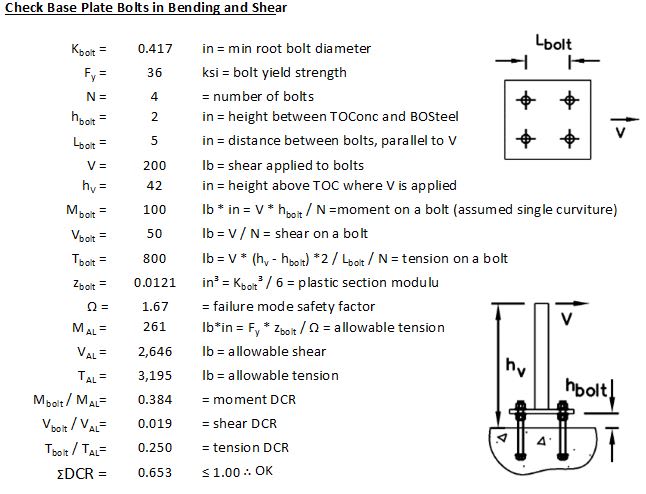