RabitPete
Structural
- Nov 24, 2020
- 109
I need to design a reinforcement to resist moment loads from the column on top of a stem wall. There is a lot of information out there on anchoring to pedestals, but not so much when it comes to rectangular footings. Concrete breakout is a controlling factor, so I am adding vertical reinforcement with loops encircling entire width of the wall on top and standard hooks at the bottom. My issue is that bottom footing is not deep enough to resist the breakout either.
What would be an effect of adding longitudinal reinforcement to the stem wall, may be make a section of it into a beam? Would it help to distribute the load from the anchors over a longer footing area, so steel which is farther away than 1/2Hef from the anchors would also contribute?
What would be an effect of adding longitudinal reinforcement to the stem wall, may be make a section of it into a beam? Would it help to distribute the load from the anchors over a longer footing area, so steel which is farther away than 1/2Hef from the anchors would also contribute?
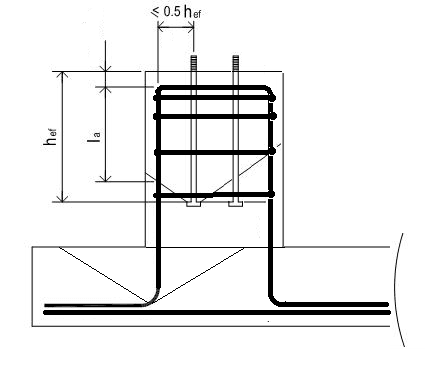