kokerkov
Mechanical
- Sep 20, 2023
- 11
Background:
We are a Chinese manufacturer that got an order of an EU client. They made a messed-up drawing, saying all tolerances as per ISO 2768-1, and need to inspect all dimensions(seems like they measured all dimensions from 3D model)
I already found angular tolerances(god, posts on the Internet about this seldomly mention it is decided by the short side of an angle), but ISO 2768-1 description about angular tolerances is strange to me:
The general orientation of the line derived from the actual sur-
face is the orientation of the contacting line of ideal geometrical
form. The maximum distance between the contacting line and
the actual line shall be the least possible value (see ISO 8015).
"
Sounds it is describing a tolerance zone as in GD&T/GPS system.
Can someone kindly explain to me how it is measured? Thanks in advance!
Plus: How can I talk to them to let them improve their drawing and requirement? Our technician told me this is not the way of doing things. Usually, people will only care about critical dimensions.
We are a Chinese manufacturer that got an order of an EU client. They made a messed-up drawing, saying all tolerances as per ISO 2768-1, and need to inspect all dimensions(seems like they measured all dimensions from 3D model)
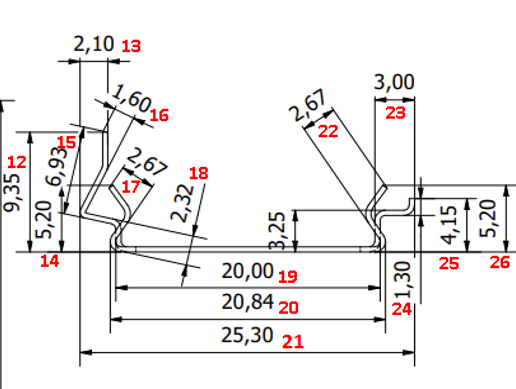
I already found angular tolerances(god, posts on the Internet about this seldomly mention it is decided by the short side of an angle), but ISO 2768-1 description about angular tolerances is strange to me:
The general orientation of the line derived from the actual sur-
face is the orientation of the contacting line of ideal geometrical
form. The maximum distance between the contacting line and
the actual line shall be the least possible value (see ISO 8015).
"
Sounds it is describing a tolerance zone as in GD&T/GPS system.
Can someone kindly explain to me how it is measured? Thanks in advance!
Plus: How can I talk to them to let them improve their drawing and requirement? Our technician told me this is not the way of doing things. Usually, people will only care about critical dimensions.