Dear experts,
A situation regarding the subject matter has emerged within a project, I am working on.
As proposed by the contractor, an API 5L Grade X52 pipe( 18", Sch 40) needs to be reviewed regarding it's compatibility with the ASTM 105 Flange (instead of ASTM A694 F60 Flange.
The discussion was open sometimes back in a thread, that's closed now.
Link
Having gone through the discussion I understand, it can be accepted and there's no issue with the compatibility.
At the same time I will appreciate, if experts can help with a code reference to the formula;
'S1 x t1 = S2 x t2, where, S1, t1 is the SMYS and the minimum thickness at the welding hub of the flange and S2 and t2 are the SMYS and nominal wall thickness of the pipe end, provided that S2/S1 ratio do not exceed 4."
Best regards,
Manisch Kumar
Piping Engineer.
A situation regarding the subject matter has emerged within a project, I am working on.
As proposed by the contractor, an API 5L Grade X52 pipe( 18", Sch 40) needs to be reviewed regarding it's compatibility with the ASTM 105 Flange (instead of ASTM A694 F60 Flange.
The discussion was open sometimes back in a thread, that's closed now.
Link
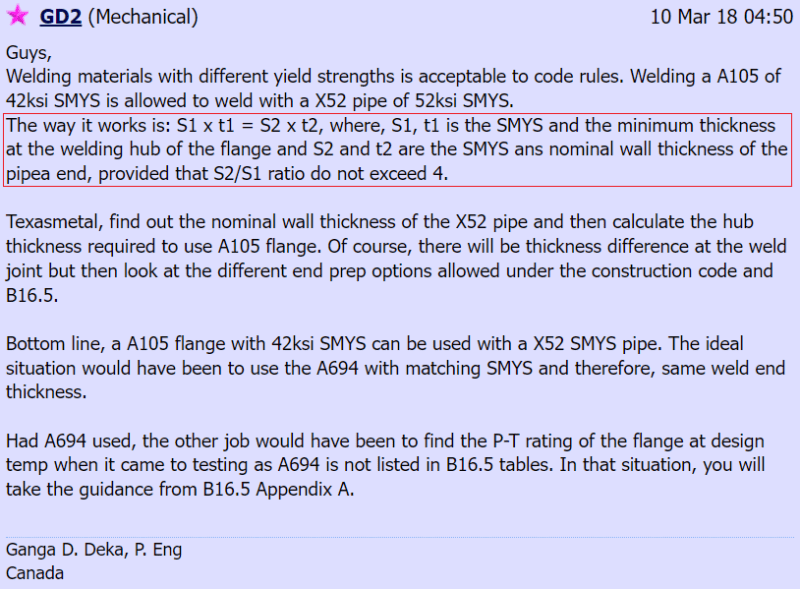
Having gone through the discussion I understand, it can be accepted and there's no issue with the compatibility.
At the same time I will appreciate, if experts can help with a code reference to the formula;
'S1 x t1 = S2 x t2, where, S1, t1 is the SMYS and the minimum thickness at the welding hub of the flange and S2 and t2 are the SMYS and nominal wall thickness of the pipe end, provided that S2/S1 ratio do not exceed 4."
Best regards,
Manisch Kumar
Piping Engineer.