goodbadgood
Materials
- Sep 24, 2014
- 40
Hi
I have 1 metallurgical sample of API 5L grade X65MS pipe.
I have done micro structure analysis and found microstructure to be granular bainite.
Let me know with your experience if my interpretation is right.
Also there is an HIC crack and in that crack i found inclusions marked by red circle. Does it look like an inclusion?
I have 1 metallurgical sample of API 5L grade X65MS pipe.
I have done micro structure analysis and found microstructure to be granular bainite.
Let me know with your experience if my interpretation is right.
Also there is an HIC crack and in that crack i found inclusions marked by red circle. Does it look like an inclusion?
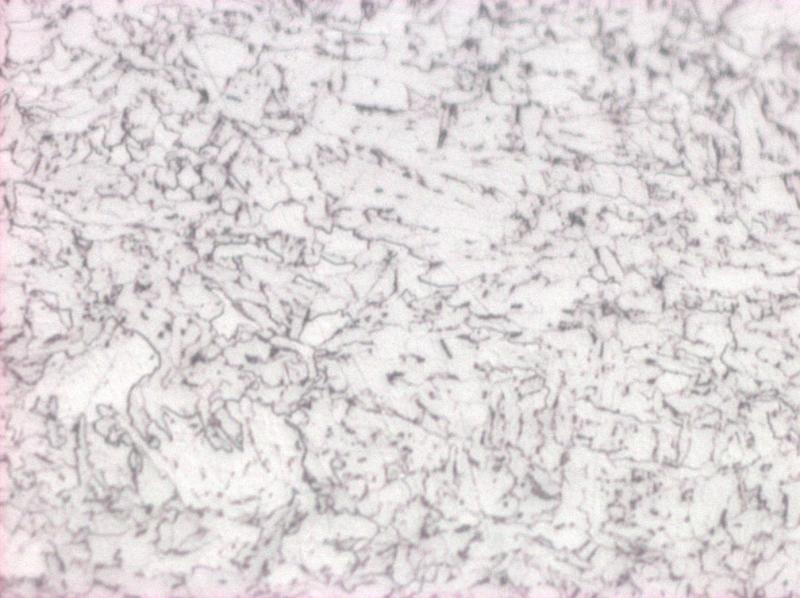
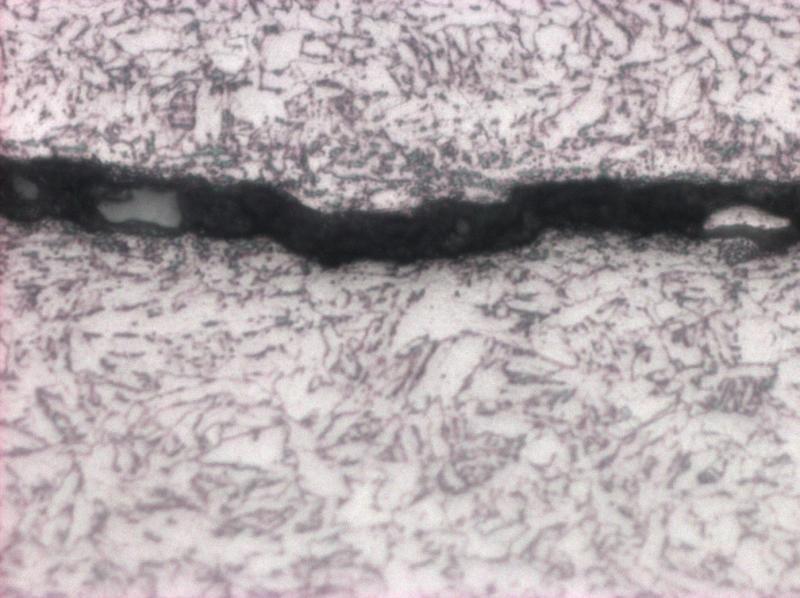