Hi,
I'm trying to model a cuboid sandwiched between two less stiff blocks, as shown in the cross-sectional view below.
This model is intended for some iterative analysis where the parts are expected to have an arbitrary level of initial overclosure. I applied a surface-to-surface, hard contact with a friction coefficient of 0.5. To resolve the overclosure automatically in a robust way, I applied an interference fit condition as well.
The model has two steps. In both steps the bottom cuboid is under encastre. a zero displacement boundary condition is applied to the top block in the initial step, which is propagated to the second step (the first analysis step). Also, in the second step, a uniformly distributed pressure is applied on top of the top block to simulate pressure on the cuboid.
The analysis would take a long time without converging and would abort in the second step (the first analysis step).
The results show stresses and strains, as expected from an interference fit, but the overclosure is not actually resolved. This is also true for all the other trials I did, with multiple meshes and boundary and loading conditions.
Any advice on how to get this analysis to converge and successfully resolve overclosure using interference fit?
Thanks
I'm trying to model a cuboid sandwiched between two less stiff blocks, as shown in the cross-sectional view below.
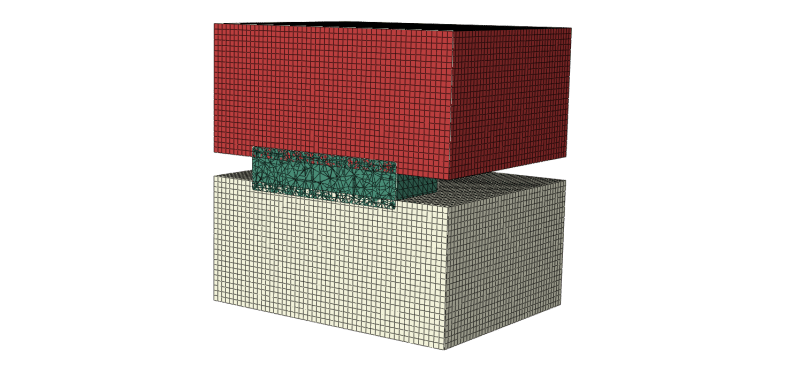
This model is intended for some iterative analysis where the parts are expected to have an arbitrary level of initial overclosure. I applied a surface-to-surface, hard contact with a friction coefficient of 0.5. To resolve the overclosure automatically in a robust way, I applied an interference fit condition as well.
The model has two steps. In both steps the bottom cuboid is under encastre. a zero displacement boundary condition is applied to the top block in the initial step, which is propagated to the second step (the first analysis step). Also, in the second step, a uniformly distributed pressure is applied on top of the top block to simulate pressure on the cuboid.
The analysis would take a long time without converging and would abort in the second step (the first analysis step).
The results show stresses and strains, as expected from an interference fit, but the overclosure is not actually resolved. This is also true for all the other trials I did, with multiple meshes and boundary and loading conditions.
Any advice on how to get this analysis to converge and successfully resolve overclosure using interference fit?
Thanks