structure_engineer
Structural
Since ASCE 7-10, the wind load is strength level for 1.0 Wind. For pipe stress calculations, do you use allowable stress design or strength level wind loads?
In COMPRESS Pressure Vessel Design Calculations, which is a Mechanical discipline related function, there is this section:
I have attached the load combinations of a vendor on a slug catcher stress calculation. It seems like they mix the strength level load factor with the nominal weight of pipe which is allowable stress design. I have no exposure to ASME B31.8. Thus, I am asking for any Piping Engineer who can help me to sort this out. I have downloaded ASME B31.8 and could not find any load combinations in the document. As far as I know, allowable stress design load combination could not be mixed with ultimate strength design load combinations. I have a set of load combinations for Load and Resistance Factor Design for structural steel members and a set of load combinations for allowable load values for pile design. There is very distinct difference between these sets of load combinations. In the attached file, should Load Combination 46 be like:
46 (OPE) W+T3+P2+0.6WIND1?
All load cases with wind load, there should be a 0.6 load factor? Your input is much appreciated. Have a Happy New Year!
In COMPRESS Pressure Vessel Design Calculations, which is a Mechanical discipline related function, there is this section:
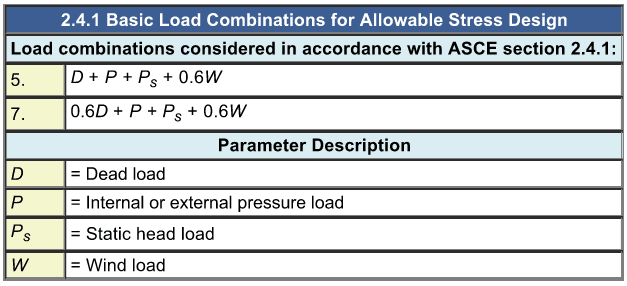
I have attached the load combinations of a vendor on a slug catcher stress calculation. It seems like they mix the strength level load factor with the nominal weight of pipe which is allowable stress design. I have no exposure to ASME B31.8. Thus, I am asking for any Piping Engineer who can help me to sort this out. I have downloaded ASME B31.8 and could not find any load combinations in the document. As far as I know, allowable stress design load combination could not be mixed with ultimate strength design load combinations. I have a set of load combinations for Load and Resistance Factor Design for structural steel members and a set of load combinations for allowable load values for pile design. There is very distinct difference between these sets of load combinations. In the attached file, should Load Combination 46 be like:
46 (OPE) W+T3+P2+0.6WIND1?
All load cases with wind load, there should be a 0.6 load factor? Your input is much appreciated. Have a Happy New Year!