KB4444
Civil/Environmental
- Nov 29, 2021
- 23
I am designing a 12.25ft lifting beam that is picked up by lifting lugs on the top flange of the beam. The lifting lugs are welded at the ends, being 12ft (144") apart, which I believe means the unbraced length would be 144"? The load is picked up by lifting lugs on the bottom of the beam spaced uniformly apart.
I am trying to size the beam in bending. Using ASME BTH-1: 3-2.3.1 Major Axis Bending of Compact Sections, I am running into a problem with the unbraced length.
I am finding that I do not have a reasonable beam size that is less then Lp (3-7) or Lr (3-10).
Using a W10x33:
Lp = 1.76 x 1.937" x sqrt(29000ksi / 50 ksi)
= 82"
Lr = sqrt(3.19 x 2.136^2 in^2 x 29000ksi x 1 / 50ksi)
[When the bending moment at any point within an unbraced length is larger than that at both end of this length, Cb shall be taken as unity. Therefore, Cb = 1.0]
= 92"
Lu = 144"?
If I am correct with Lu being the space between supports what is my next step? I wouldn't have Lu < Lr, so I believe I am stuck going to an even larger beam size? The bending stress in this situation wouldn't govern.
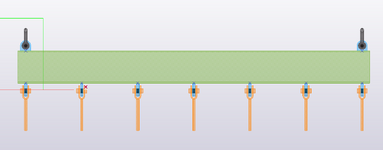
I am trying to size the beam in bending. Using ASME BTH-1: 3-2.3.1 Major Axis Bending of Compact Sections, I am running into a problem with the unbraced length.
I am finding that I do not have a reasonable beam size that is less then Lp (3-7) or Lr (3-10).
Using a W10x33:
Lp = 1.76 x 1.937" x sqrt(29000ksi / 50 ksi)
= 82"
Lr = sqrt(3.19 x 2.136^2 in^2 x 29000ksi x 1 / 50ksi)
[When the bending moment at any point within an unbraced length is larger than that at both end of this length, Cb shall be taken as unity. Therefore, Cb = 1.0]
= 92"
Lu = 144"?
If I am correct with Lu being the space between supports what is my next step? I wouldn't have Lu < Lr, so I believe I am stuck going to an even larger beam size? The bending stress in this situation wouldn't govern.
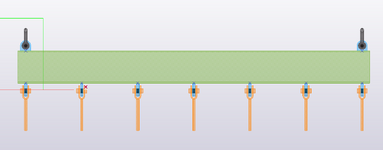