I'm working on a project involving a stainless steel ASME vessel rated for 120 psig designed to Section VIII Div 1. While doing the piping design, we identified high forces/moments on this 3" nozzle due to relief forces.
We sent the loads to the vessel vendor to try to confirm the nozzle is okay and/or propose reinforcement, but they basically said they can't run the numbers. They further stated the maximum bending moment this flange can withstand is approximately 19 ft-lbs, limited by the Class 150 flange and governed by MAWP reduction due to external load in their software. He said it'd need to be a Class 900 flange for the moments we were showing.
I'm not an ASME pressure vessel code guy but the 19 ft-lb response seems absurdly low to me. We're pursuing FEA analysis and preliminary results seem to be indicating a minor repad will be needed due to stresses at the head connection, but no concerns about the flange itself. Does this make sense and Div 1 is just absurdly conservative in this regard? It feels like we're missing something.
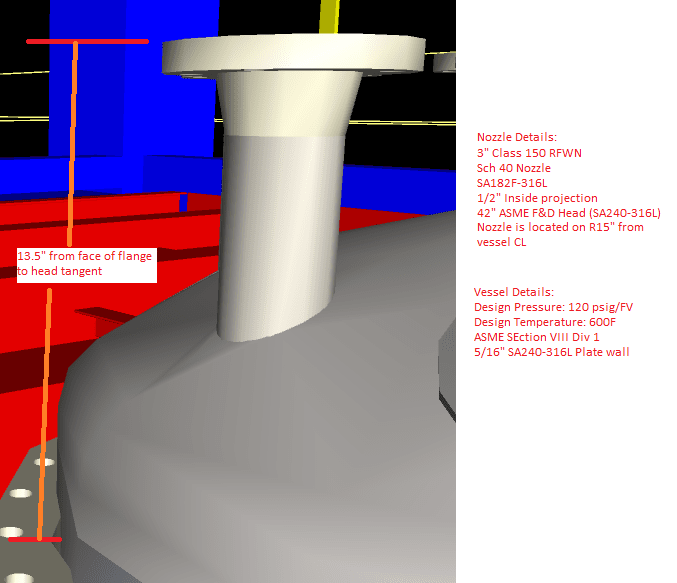
We sent the loads to the vessel vendor to try to confirm the nozzle is okay and/or propose reinforcement, but they basically said they can't run the numbers. They further stated the maximum bending moment this flange can withstand is approximately 19 ft-lbs, limited by the Class 150 flange and governed by MAWP reduction due to external load in their software. He said it'd need to be a Class 900 flange for the moments we were showing.
I'm not an ASME pressure vessel code guy but the 19 ft-lb response seems absurdly low to me. We're pursuing FEA analysis and preliminary results seem to be indicating a minor repad will be needed due to stresses at the head connection, but no concerns about the flange itself. Does this make sense and Div 1 is just absurdly conservative in this regard? It feels like we're missing something.