Hi everybody,
I'm a mechanical engineer trying to wrap my head around choosing a transformer for a new CNC mill coming into our shop. We're a small operation, so I have ownership of all the technical aspects of the purchase, nearly all of which are squarely within my professional experience. The 3-phase power, however, is a new frontier.
Of course, a real electrician will perform the installation, but I need to have a fundamental understanding of the situation in order to get quotes for the work. Also, the machine represents a significant investment for our shop, so we're proceeding very methodically.
Documentation provided by the machine tool maker seems weak, at least to a layman. A call to the applications department of a transformer manufacturer was little help. Most surprising is the amount of bad and dangerous advice online regarding machine tool wiring.
I greatly appreciate any education that you can provide. Please correct any errors of terminology without mercy. So, here's our situation:
[li]Power company will supply our facility with 277/480 3-phase 4-wire wye.[/li]
[li]Machine tool specs name a range of acceptable input voltage that is nominally referred to as 220 3-phase.[/li]
[li]Machine peak power is 40kVA, maximum continuous power is 28 kVA. I'd guess that most people never use these machines at anywhere near these levels; we certainly won't.[/li]
[li]We're considering a transformer rated for 75kVA to support future machine purchases.[/li]
The following points are taken directly from the machine tool documentation:
[ol 1]
[li]The ground wire is required for operator safety and correct operation.[/li]
[li]A separate ground wire must be connected to the chassis of the machine.[/li]
[li]The ground wire must be supplied from the main building ground.[/li]
[li]Do not use a conduit as a ground wire.[/li]
[li]Do not use a cold-water pipe or ground rod to supply the machine ground buss[/li]
[li]Power can be Wye or Delta type.[/li]
[li]You must ground the power source. One leg or center leg for Delta. Neutral for Wye.[/li]
[/ol]
I wish that their language was a bit more precise or that they provided a diagram. In any case, as a layman with little knowledge of the applicable NEC requirements, I draw the following conclusions:
[ol 1]
[li]Transformer secondary could be either wye or delta.[/li]
[li]With a wye secondary, the center of the wye should be bonded to the equipment grounding conductor (EGC).[/li]
[li]With a delta secondary, either the center of one phase or the corner should be bonded to the EGC.[/li]
[li]The machine does not require a specific voltage between any phase and the ground lug of the machine.[/li]
[li]The EGC should be a wire and should run directly to the ground lug of the machine.[/li]
[/ol]
These conclusions lead to more questions:
[ol 1]
[li]It seems like there is no purpose for a "neutral" coming from the secondary of the transformer. Is this correct?[/li]
[li]Is there a reason to choose a particular primary arrangement, delta or wye?[/li]
[li]Is there a reason to choose a particular secondary arrangement, either delta or wye?[/li]
[li]If a delta secondary is chosen, since I don't need a particular phase-to-neutral voltage, is there a preferred method of bonding to the EGC, either center-of-phase or corner?[/li]
[/ol]
This post is getting awfully long, so let me stop here for now. I have attached a diagram of my understanding of the situation. I welcome harsh criticism of that as well.
I appreciate your help!
I'm a mechanical engineer trying to wrap my head around choosing a transformer for a new CNC mill coming into our shop. We're a small operation, so I have ownership of all the technical aspects of the purchase, nearly all of which are squarely within my professional experience. The 3-phase power, however, is a new frontier.
Of course, a real electrician will perform the installation, but I need to have a fundamental understanding of the situation in order to get quotes for the work. Also, the machine represents a significant investment for our shop, so we're proceeding very methodically.
Documentation provided by the machine tool maker seems weak, at least to a layman. A call to the applications department of a transformer manufacturer was little help. Most surprising is the amount of bad and dangerous advice online regarding machine tool wiring.
I greatly appreciate any education that you can provide. Please correct any errors of terminology without mercy. So, here's our situation:
[li]Power company will supply our facility with 277/480 3-phase 4-wire wye.[/li]
[li]Machine tool specs name a range of acceptable input voltage that is nominally referred to as 220 3-phase.[/li]
[li]Machine peak power is 40kVA, maximum continuous power is 28 kVA. I'd guess that most people never use these machines at anywhere near these levels; we certainly won't.[/li]
[li]We're considering a transformer rated for 75kVA to support future machine purchases.[/li]
The following points are taken directly from the machine tool documentation:
[ol 1]
[li]The ground wire is required for operator safety and correct operation.[/li]
[li]A separate ground wire must be connected to the chassis of the machine.[/li]
[li]The ground wire must be supplied from the main building ground.[/li]
[li]Do not use a conduit as a ground wire.[/li]
[li]Do not use a cold-water pipe or ground rod to supply the machine ground buss[/li]
[li]Power can be Wye or Delta type.[/li]
[li]You must ground the power source. One leg or center leg for Delta. Neutral for Wye.[/li]
[/ol]
I wish that their language was a bit more precise or that they provided a diagram. In any case, as a layman with little knowledge of the applicable NEC requirements, I draw the following conclusions:
[ol 1]
[li]Transformer secondary could be either wye or delta.[/li]
[li]With a wye secondary, the center of the wye should be bonded to the equipment grounding conductor (EGC).[/li]
[li]With a delta secondary, either the center of one phase or the corner should be bonded to the EGC.[/li]
[li]The machine does not require a specific voltage between any phase and the ground lug of the machine.[/li]
[li]The EGC should be a wire and should run directly to the ground lug of the machine.[/li]
[/ol]
These conclusions lead to more questions:
[ol 1]
[li]It seems like there is no purpose for a "neutral" coming from the secondary of the transformer. Is this correct?[/li]
[li]Is there a reason to choose a particular primary arrangement, delta or wye?[/li]
[li]Is there a reason to choose a particular secondary arrangement, either delta or wye?[/li]
[li]If a delta secondary is chosen, since I don't need a particular phase-to-neutral voltage, is there a preferred method of bonding to the EGC, either center-of-phase or corner?[/li]
[/ol]
This post is getting awfully long, so let me stop here for now. I have attached a diagram of my understanding of the situation. I welcome harsh criticism of that as well.
I appreciate your help!
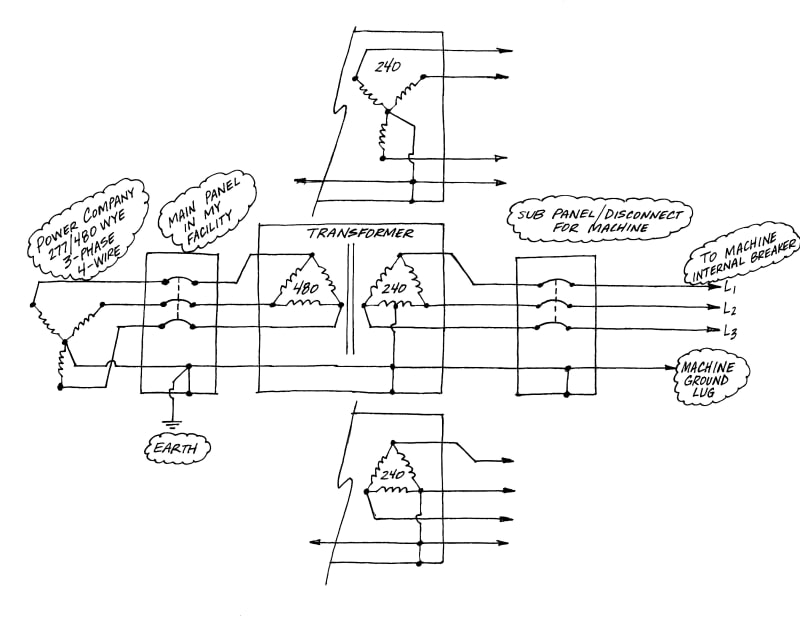