ElronMcK
Structural
- Oct 2, 2020
- 20
I am trying to get certified in TIG aluminum 6061 3G per D1.2 4043, up to 3/8" or 1/4" thick plate, and I am looking for guidance. I am trying to diversify my credentials for more job options.
[I am a steel guy and am certified 3G D1.1. Not ASME. Almost everyone I know is a steel guy. Aluminum structural welding is rare in my world, but occasional happens, usually not be a certified alum welder. I am semi-confident welding 60xx, but don't personally know a D1.2 certified aluminum welder - they must be in different industries (aerospace?). This question is not for steel guys.]
1. If I want to be certified for up to 3/8" 6061 plate, then I need to test on 3/16" thick plate, I think. From the D1.2 figures, it appears that the test plate surface would need to be milled down to 1/8" after welding, then cut the coupon strips, then bend test.
a. prep plates and fit up
b. weld plate in 60 degree V joint
c. visual inspection by CWI
d. mill 3/16" thk plate down to 1/8" (this is the unusual part for me)
e. cut 1.5" wide strips
f. face and root bend tests
Am I understanding this right?
2. I might just go with 1/8" thick test plate and butt joint (to be qualified for up to 1/4" thick plate). Post-milling not required. I can get near perfect penetration welding from one side only with a no-gap butt joint. However, I nervous about failing the bend test without a double sided weld. Is there any problem welding from one side, grinding the backside, then final pass on backside?
3. If I pass 1/8" groove test, I am certified for any thickness fillet weld?
I'm not getting much guidance from the CWI either. He's also a steel guy.
*I previously posted this on the Welding, Bonding & Fastening Forum, but got zero responses, so I removed and re-directed here*
[I am a steel guy and am certified 3G D1.1. Not ASME. Almost everyone I know is a steel guy. Aluminum structural welding is rare in my world, but occasional happens, usually not be a certified alum welder. I am semi-confident welding 60xx, but don't personally know a D1.2 certified aluminum welder - they must be in different industries (aerospace?). This question is not for steel guys.]
1. If I want to be certified for up to 3/8" 6061 plate, then I need to test on 3/16" thick plate, I think. From the D1.2 figures, it appears that the test plate surface would need to be milled down to 1/8" after welding, then cut the coupon strips, then bend test.
a. prep plates and fit up
b. weld plate in 60 degree V joint
c. visual inspection by CWI
d. mill 3/16" thk plate down to 1/8" (this is the unusual part for me)
e. cut 1.5" wide strips
f. face and root bend tests
Am I understanding this right?
2. I might just go with 1/8" thick test plate and butt joint (to be qualified for up to 1/4" thick plate). Post-milling not required. I can get near perfect penetration welding from one side only with a no-gap butt joint. However, I nervous about failing the bend test without a double sided weld. Is there any problem welding from one side, grinding the backside, then final pass on backside?
3. If I pass 1/8" groove test, I am certified for any thickness fillet weld?
I'm not getting much guidance from the CWI either. He's also a steel guy.
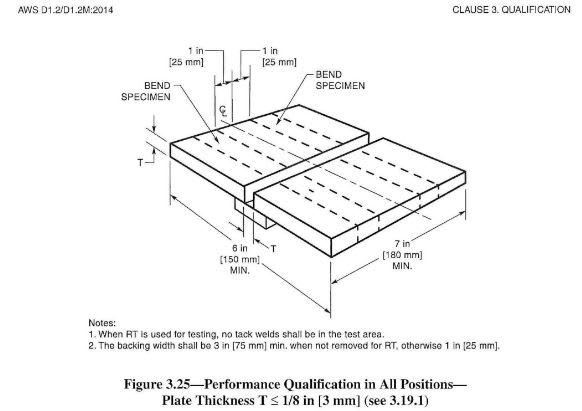
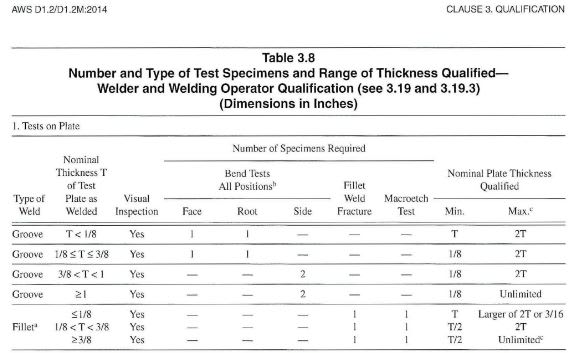
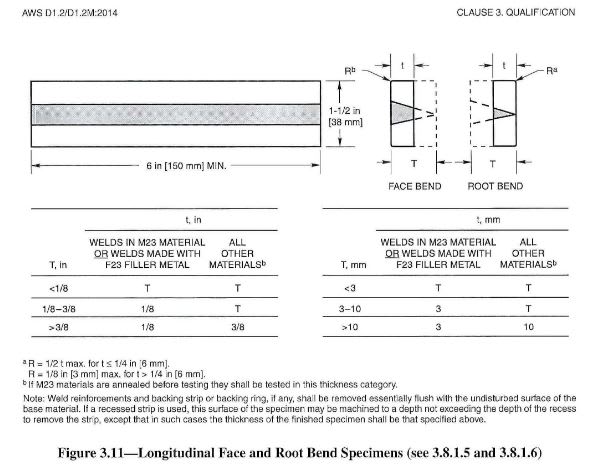
*I previously posted this on the Welding, Bonding & Fastening Forum, but got zero responses, so I removed and re-directed here*