Hello dear
I hope it is the correct forum to discus the below question
I insert a shaft to a hub according to image below, then I could calculat the friction coefficient from insertion force. This assmbly is based on the interference insertion.
After shaft insertion I need to calculate the highest torque that the shaft can withstand in the hub.
My question is if the friction coefficient from shaft insertion is valid to use for calculating the torque?
Thanks in advance for your time and your knowledge.
I hope it is the correct forum to discus the below question
I insert a shaft to a hub according to image below, then I could calculat the friction coefficient from insertion force. This assmbly is based on the interference insertion.
After shaft insertion I need to calculate the highest torque that the shaft can withstand in the hub.
My question is if the friction coefficient from shaft insertion is valid to use for calculating the torque?
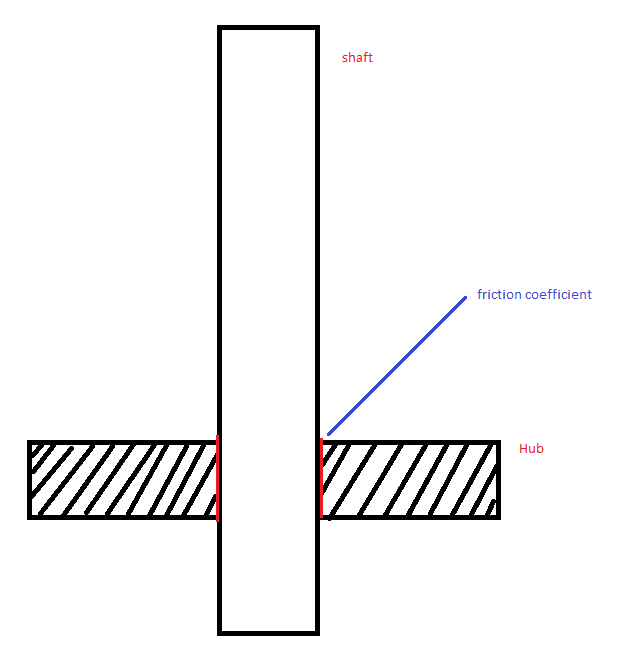
Thanks in advance for your time and your knowledge.