rQuestionEngineering
Mechanical
- Aug 30, 2012
- 204
Below shows axle bolt design
Which is more superior and cheaper ?
Which is more superior and cheaper ?
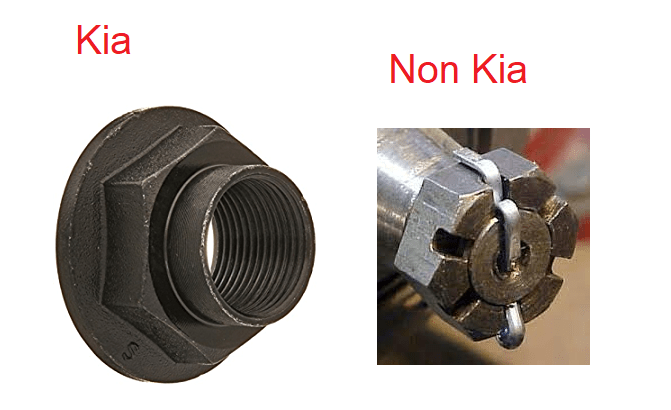
Follow along with the video below to see how to install our site as a web app on your home screen.
Note: This feature may not be available in some browsers.